Electrical Discharge Machining (EDM)
Transforming Precision Manufacturing
Electrical Discharge Machining (EDM) is a cutting-edge precision technology that has reshaped the manufacturing landscape.
Known for its ability to create microscopic, highly accurate holes in even the hardest materials, EDM small hole drilling
has become indispensable across industries where precision, durability, and innovation are non-negotiable. From aerospace
turbine blades and biomedical devices to automotive fuel injectors, EDM consistently delivers unmatched performance for
the most demanding machining challenges. In this page, we’ll explore the wide-ranging applications of EDM and how it continues
to drive innovation in modern engineering.
Why EDM Small Hole Drilling Is Essential
EDM small hole drilling stands out as a revolutionary machining process for its unique ability to create precise holes
in materials that are traditionally hard to machine. Its distinct advantages make it the preferred choice for industries
requiring high-performance components. Key benefits include:
- Precision and Accuracy: EDM achieves unparalleled accuracy, drilling microscopic holes with consistent dimensions, critical for applications like fuel injectors and turbine blades.
- Machining Tough Materials: The non-contact nature of EDM allows it to penetrate hard materials such as tungsten carbide, Hastelloy, and Inconel without deformation.
- No Tool Pressure: Unlike conventional machining, EDM eliminates physical tool pressure, making it ideal for delicate components and reducing the risk of burrs or mechanical stresses.
- Versatility Across Industries: Whether it’s aerospace, biomedical, or automotive, EDM small hole drilling adapts to complex designs and extreme material requirements.
Key Industry Applications of EDM Small Hole Drilling
EDM small hole drilling has revolutionized several industries by providing unmatched precision and adaptability.
Below are the key industries where EDM plays a critical role:
Aerospace
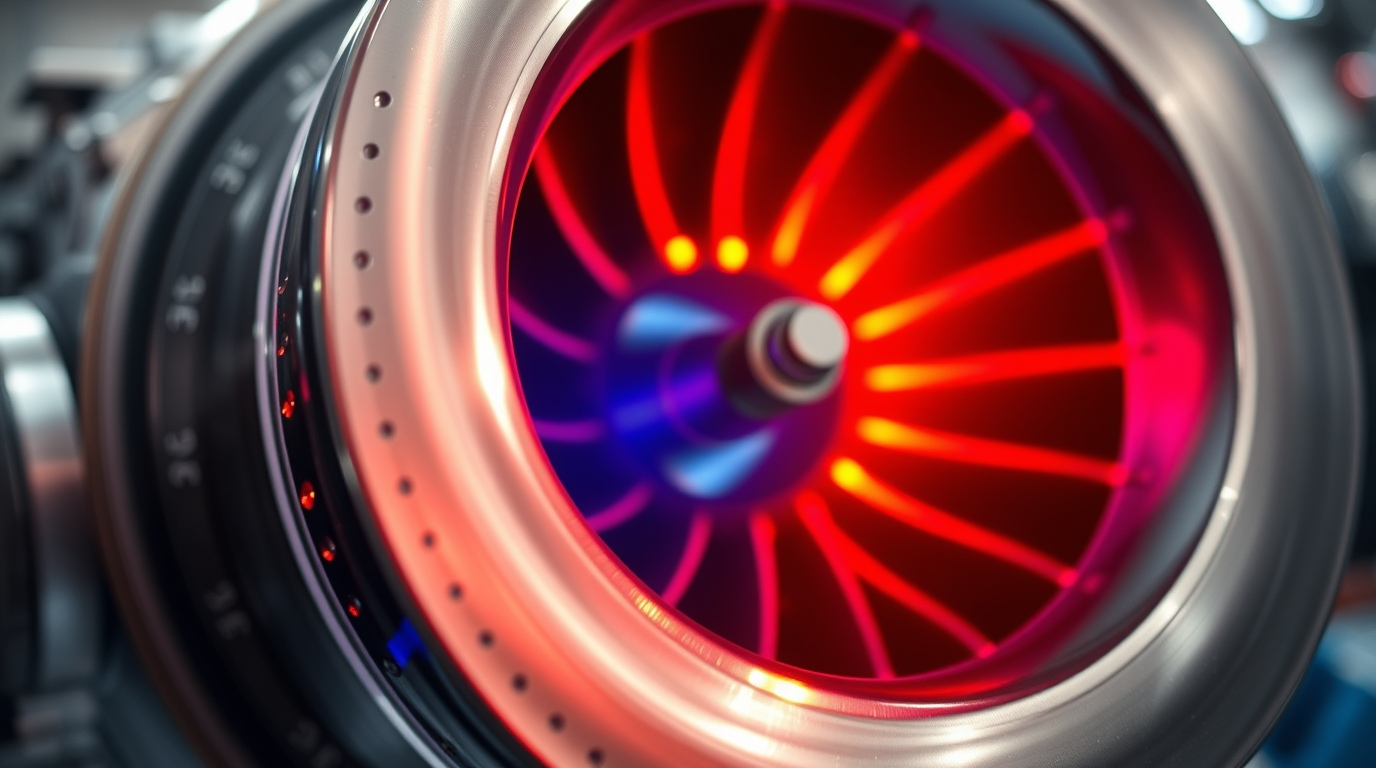
Electrical Discharge Machining (EDM) is crucial in aerospace applications where precise hole drilling is required for high-temperature, high-pressure environments.
Components such as turbine blades, combustion chambers, and fuel nozzle holes rely on EDM for optimal performance and efficiency.
- Turbine blade film cooling holes: Ensures jet engines and gas turbines can endure temperatures exceeding 2000 Kelvin.
- Combustion liners: Precisely drilled holes to maintain efficiency and safety under extreme conditions.
- Combustion chambers: Microscopic nozzles that manage air and fuel flow.
- Fuel nozzle holes: Ensures optimal fuel atomization for efficiency and reduced emissions.
- Rocket engine injectors: EDM creates microscopic nozzles for precise fuel and oxidizer injection.
Gas turbine engines operate at extreme temperatures, which can compromise the integrity of engine blades. Film cooling, achieved by bleeding cool air from the compressor through internal chambers and out of EDM-drilled cooling holes, forms cooling jets that reduce convective heat transfer. This ensures turbine blades remain operable and efficient. EDM electrodes are critical to the precision required for these intricate cooling holes.
Medical
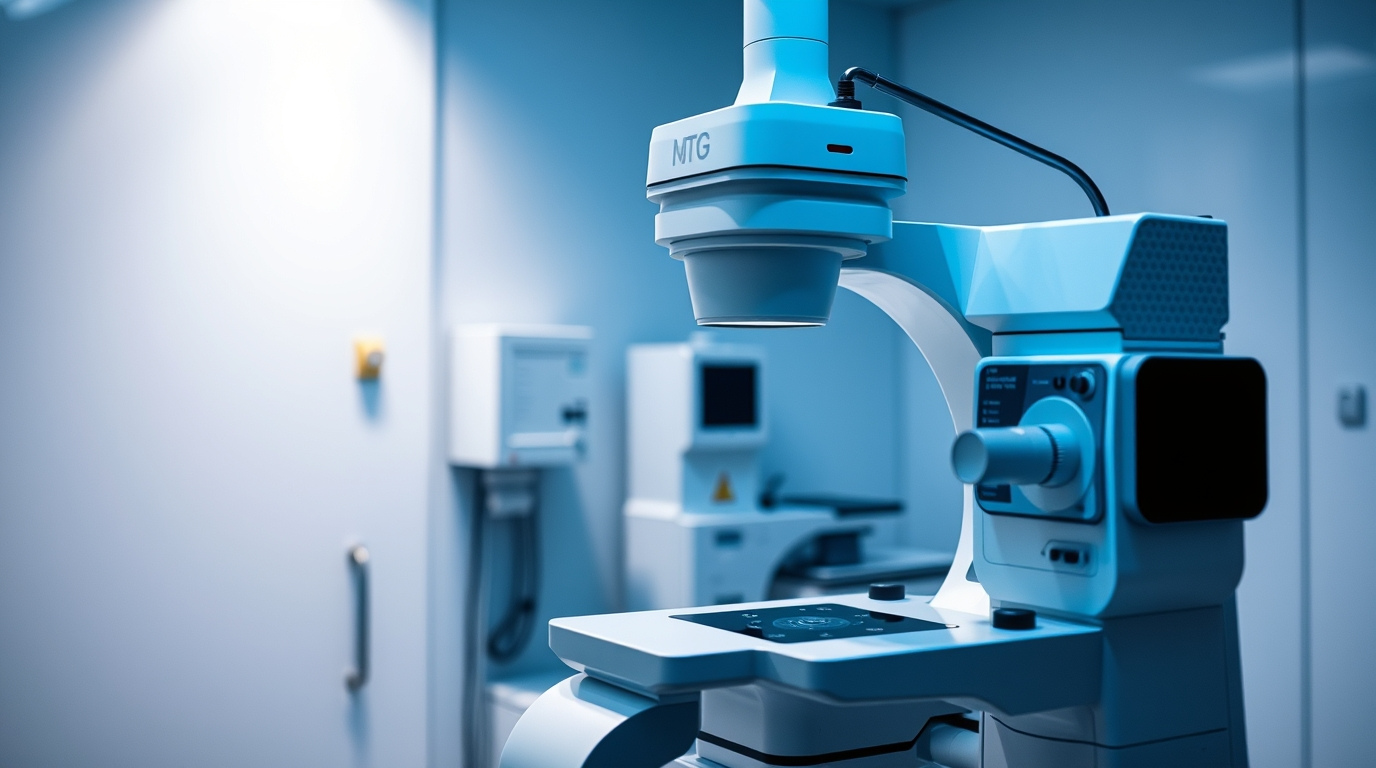
Electrical Discharge Machining (EDM) plays a critical role in manufacturing small, complex parts for medical devices. With extreme precision,
EDM is used to create holes and cavities in intricate components that are vital to life-saving and diagnostic equipment.
- Artificial heart valves and stents: Precision-machined components ensuring reliability and safety.
- Micro cross holes in catheters: Allow for controlled flow and pressure, critical for medical procedures.
- Medical implants: Intricate holes and cavities in titanium or other materials for precision fit and function.
- Surgical instruments: Stainless steel and titanium instruments that meet the highest standards for precision and reliability.
- Medical diagnostic equipment: Sensors and accessible integration points for advanced healthcare devices.
EDM ensures that medical devices meet strict regulatory and functional standards by providing unmatched precision for small and intricate parts. From machining tiny holes in catheters to crafting components for artificial hearts, EDM is essential for advancing modern medicine.
Defense
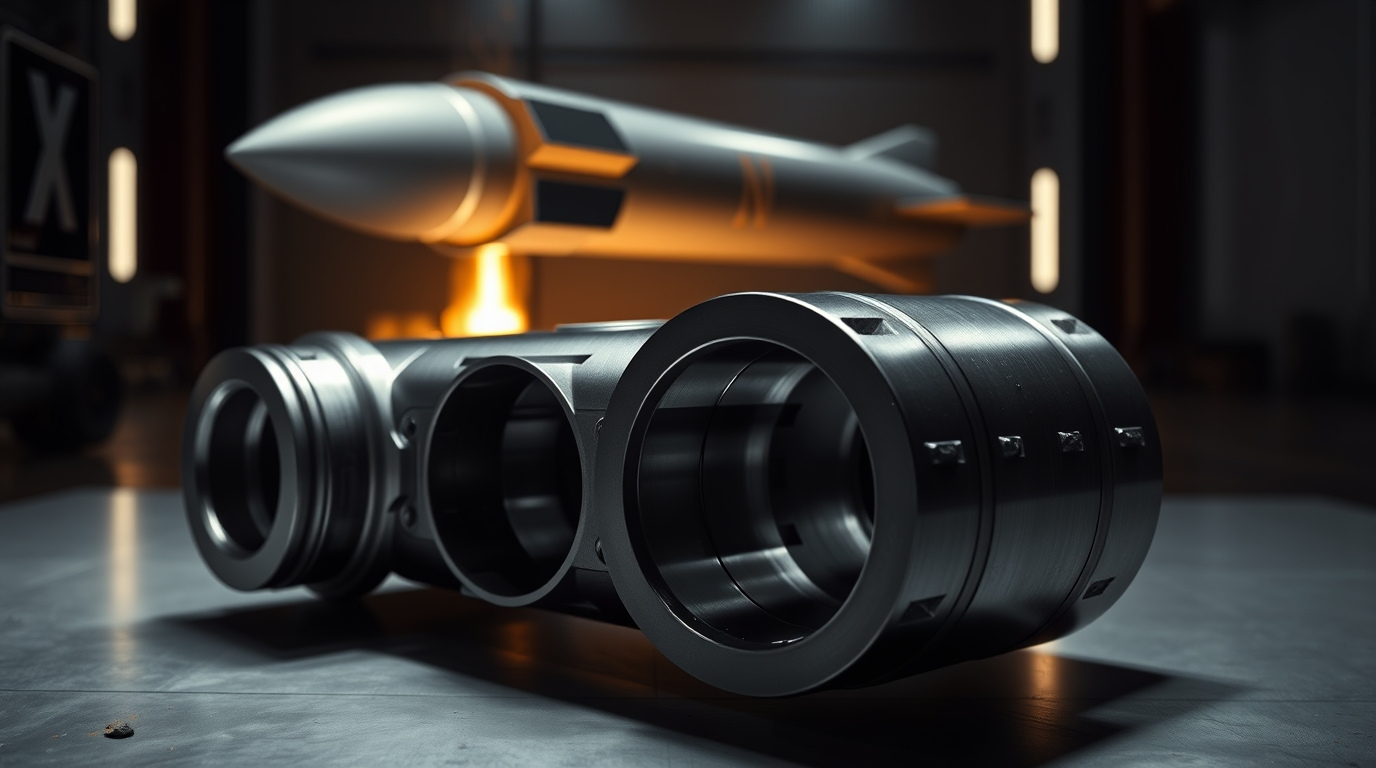
Electrical Discharge Machining (EDM) is an indispensable technology in the defense industry, where precision, durability, and reliability are paramount.
From advanced weaponry to critical system components, EDM ensures high-performance machining for components that operate under extreme conditions.
- Weapon system components: EDM is used to manufacture precision parts for advanced weapons, including missile guidance systems and targeting devices.
- Ammunition components: Machined holes and cavities in shells and casings ensure optimal performance and reliability.
- Armored vehicle components: EDM is ideal for machining intricate parts used in tanks and military vehicles, ensuring durability in rugged environments.
- Aerospace defense systems: Precision-machined nozzles and housings for missiles, UAVs, and aircraft components.
- Electronic and radar systems: Delicate EDM-machined components support high-precision radar and communication systems.
Defense systems require precision machining for critical components that often face extreme temperatures, pressures, and mechanical stresses. EDM’s non-contact process eliminates mechanical stress on delicate parts, ensuring burr-free finishes and unparalleled accuracy.
Whether creating intricate cavities in missile casings or precision nozzles for aerospace applications, EDM provides the reliability needed for high-stakes defense operations.
Power Generation
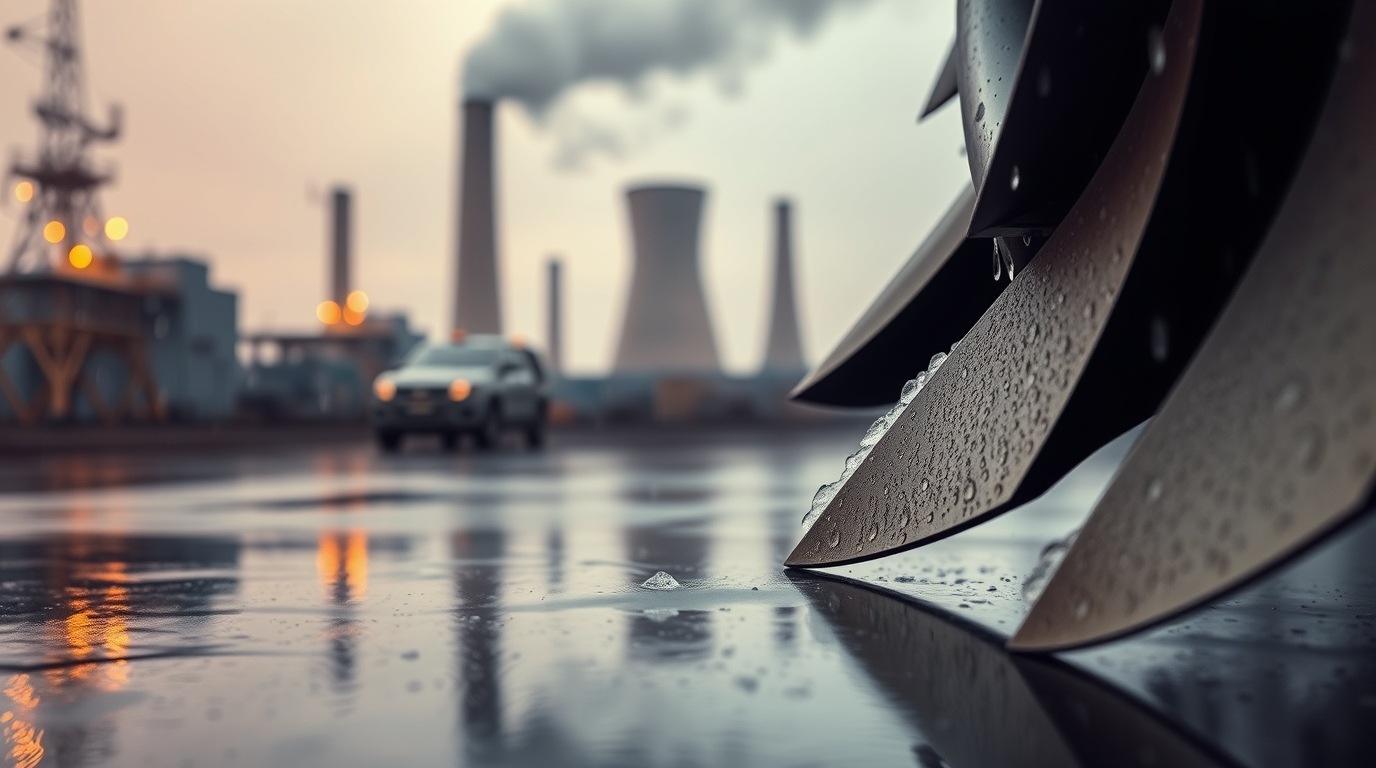
Electrical Discharge Machining (EDM) is a key technology in power generation industries, where components must endure extreme temperatures, pressures, and mechanical stresses.
EDM is used to create intricate features and precise holes in components critical for power plants, gas turbines, and nuclear systems.
- Gas turbine cooling holes: EDM drills intricate cooling channels in turbine blades to maintain efficiency and prevent overheating.
- Combustion chambers: Precision-machined holes allow for optimized airflow and combustion processes in power generation systems.
- Nuclear reactor components: EDM is used for machining radiation-resistant materials and creating precise, burr-free cavities.
- Steam turbine parts: Machined components that ensure durability and performance under high-pressure environments.
- Generator cooling systems: Precision drilling in cooling plates and heat exchangers for efficient thermal management.
Power generation systems demand precision and reliability to operate efficiently in harsh environments. EDM ensures that components like turbine blades, combustion chambers, and cooling systems meet exacting standards for durability and performance.
Whether for gas turbines or nuclear reactors, EDM’s ability to machine hard materials with unparalleled accuracy makes it indispensable for the power generation industry.
Laboratory & Research
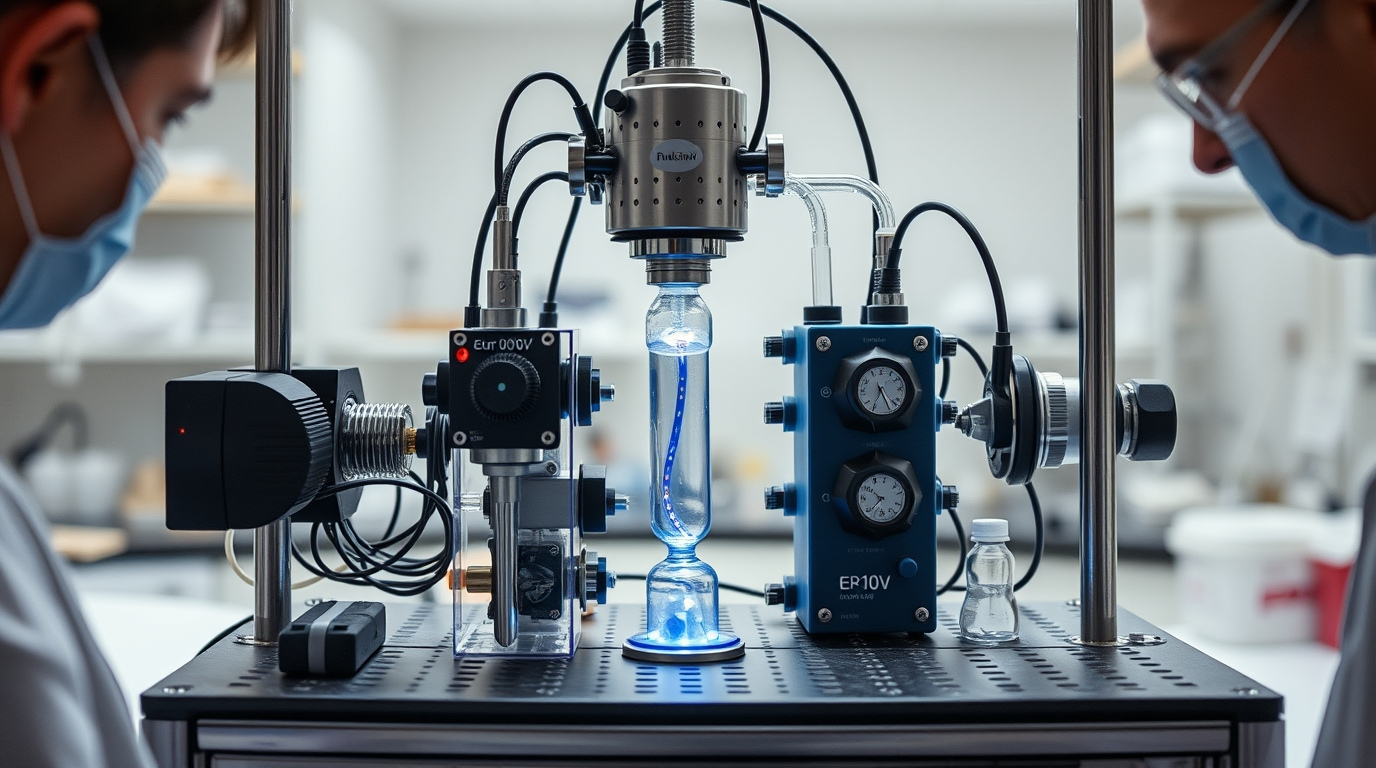
Electrical Discharge Machining (EDM) is integral to laboratories and research facilities where precision and accuracy are paramount. From crafting components for scientific equipment to prototyping experimental designs, EDM enables researchers to push the boundaries of innovation.
- Precision experimental components: EDM creates intricate parts for experimental setups, ensuring high accuracy and repeatability.
- Prototyping advanced materials: Machining prototypes for new materials or devices with exacting tolerances.
- Scientific instruments: Precision-drilled components for spectrometers, microscopes, and other laboratory tools.
- Material testing devices: EDM-machined parts for equipment used to analyze material properties under extreme conditions.
- Microscale research: EDM enables fabrication of tiny holes and features for microfluidic systems and nanoscale experiments.
EDM’s ability to machine hard-to-work materials like titanium, stainless steel, and exotic alloys makes it indispensable for cutting-edge research. Whether designing experimental setups, manufacturing intricate parts, or developing prototypes, EDM provides the precision and flexibility required for the most demanding scientific applications.
Nuclear & Atomic
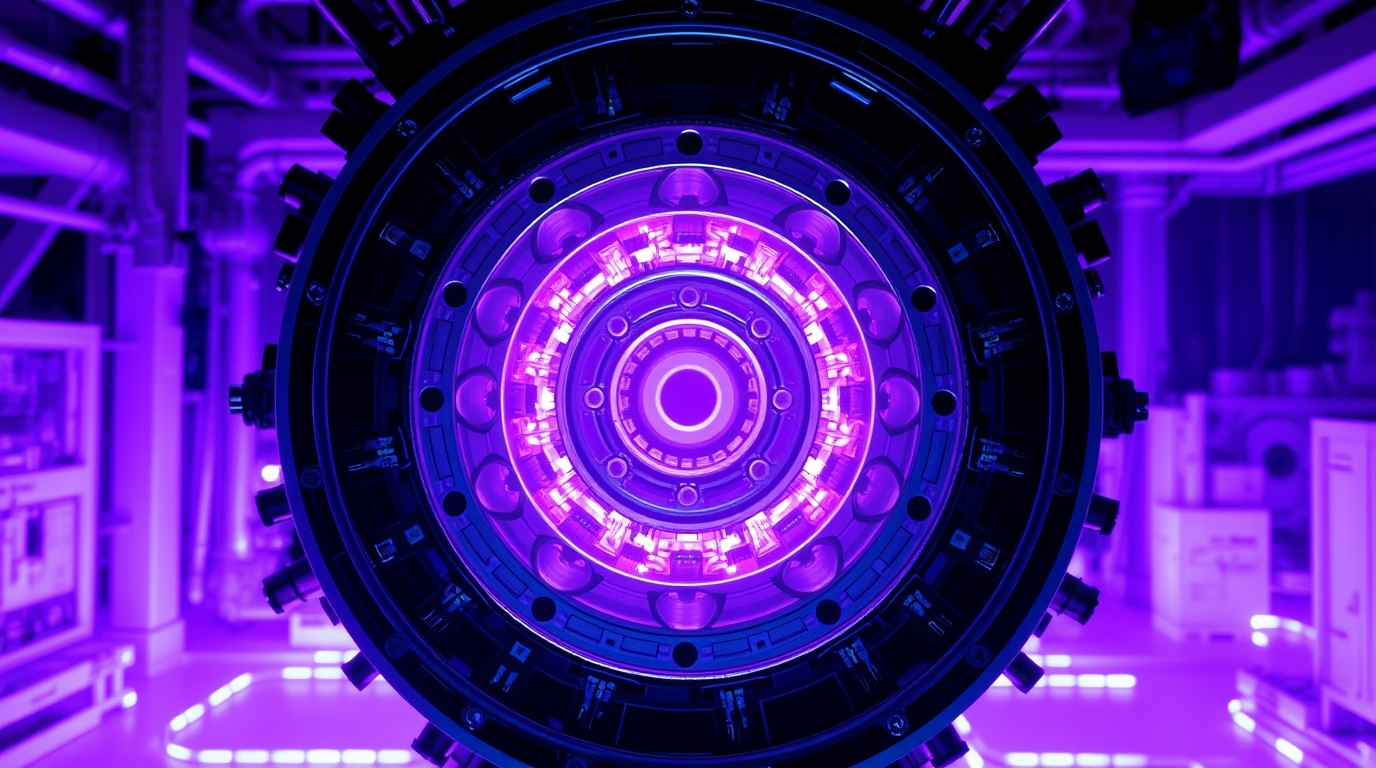
Electrical Discharge Machining (EDM) is essential in the nuclear and atomic industries, where precision, durability, and resistance to extreme conditions are paramount.
EDM allows for the creation of intricate and radiation-resistant components critical to nuclear reactors, atomic research, and energy generation.
- Radiation-resistant materials: EDM machines components made of specialized alloys designed to withstand high radiation exposure.
- Fuel rod assemblies: Precision holes and grooves in fuel rod components ensure proper fit and function in reactors.
- Control rod mechanisms: Accurate machining of control rod components for safe and efficient reactor operation.
- Heat exchangers and cooling systems: Precision drilling in plates and tubes for thermal regulation in nuclear plants.
- Containment vessel components: Machined parts that maintain structural integrity under extreme pressure and temperature.
Nuclear and atomic systems require machining processes that can handle high-strength materials such as Inconel, Hastelloy, and zirconium alloys. EDM’s non-contact process ensures precise, burr-free machining, making it indispensable for components used in high-radiation and high-temperature environments.
From crafting fuel assemblies to control rods, EDM provides the precision and reliability necessary for critical nuclear operations.
Manufacturing
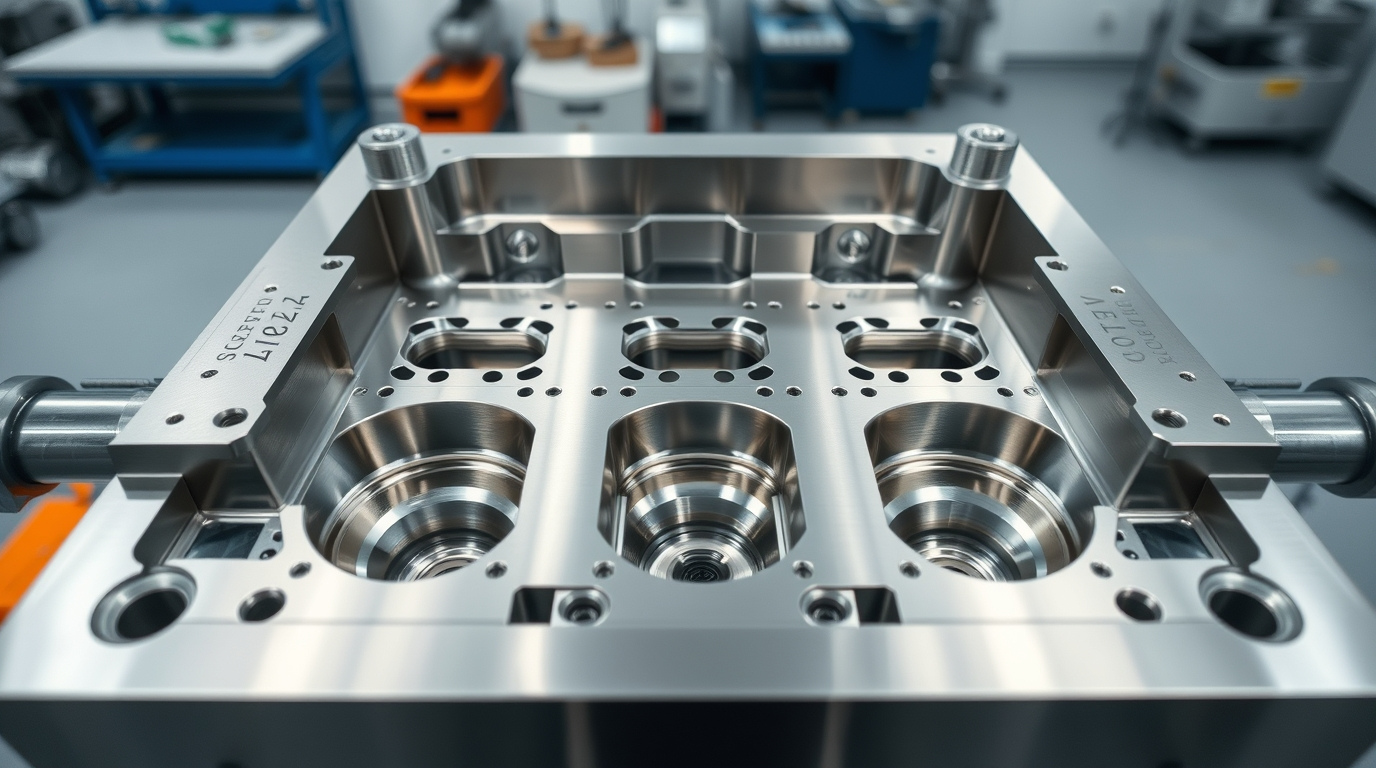
Electrical Discharge Machining (EDM) is a vital technology in the manufacturing industry, enabling the production of precise components used in industrial-scale production. From injection molds to synthetic fiber spinnerets, EDM plays a critical role in crafting intricate parts that meet exacting standards for modern manufacturing.
- Injection molds: EDM creates runner holes, gates, and intricate cavities used to channel molten material into molds for plastic and metal parts.
- Die casting: Machined components for die-cast molds ensure smooth flow paths for molten metal, reducing defects and improving production efficiency.
- Spinnerets for synthetic fibers: Precision-drilled arrays of tiny holes for producing consistent strands of polyester, nylon, and other synthetic materials.
- Cutting tools: EDM is used to machine cooling channels in drill bits, saw blades, and other tools for enhanced performance and durability.
- Industrial machinery components: Precision parts for machinery, such as housings, gears, and fittings, ensure optimal performance and longevity.
Modern manufacturing relies on EDM to machine hard-to-work materials like titanium, tungsten carbide, and hardened steels. With unmatched precision and the ability to create intricate patterns, EDM supports industries ranging from automotive and aerospace to textiles and heavy machinery. By delivering accuracy and efficiency, EDM continues to revolutionize industrial production.
Benefits of EDM Small Hole Drilling
EDM small hole drilling stands out for its precision, adaptability, and ability to tackle challenging materials.
Its unique advantages make it a preferred machining method across industries:
- Unmatched Precision: EDM can create micro-holes with exact dimensions and tolerances, ensuring consistent performance in critical applications such as fuel injectors and turbine cooling holes.
- Machining Tough Materials: With the ability to drill through hard materials like tungsten carbide, Hastelloy, and Inconel, EDM expands what’s possible in modern manufacturing.
- No Physical Tool Pressure: As a non-contact process, EDM avoids physical tool pressure, reducing the risk of deformation, burrs, or mechanical damage on delicate or complex workpieces.
- Burr-Free Holes: The process ensures clean, burr-free holes that eliminate the need for additional finishing operations.
- Versatility Across Applications: From aerospace components to medical devices, EDM’s adaptability supports diverse industries and design requirements.
- High Repeatability: EDM guarantees consistent results, even for high-volume production, making it ideal for precision manufacturing at scale.
Suggested Image: A close-up of an EDM machine in action or a finished product (e.g., a turbine blade with visible cooling holes).
Electrode Types for Different Applications
EDM small hole drilling owes much of its versatility to the variety of electrode materials available. Each type of electrode is tailored to meet specific machining requirements, ensuring optimal performance across different applications.
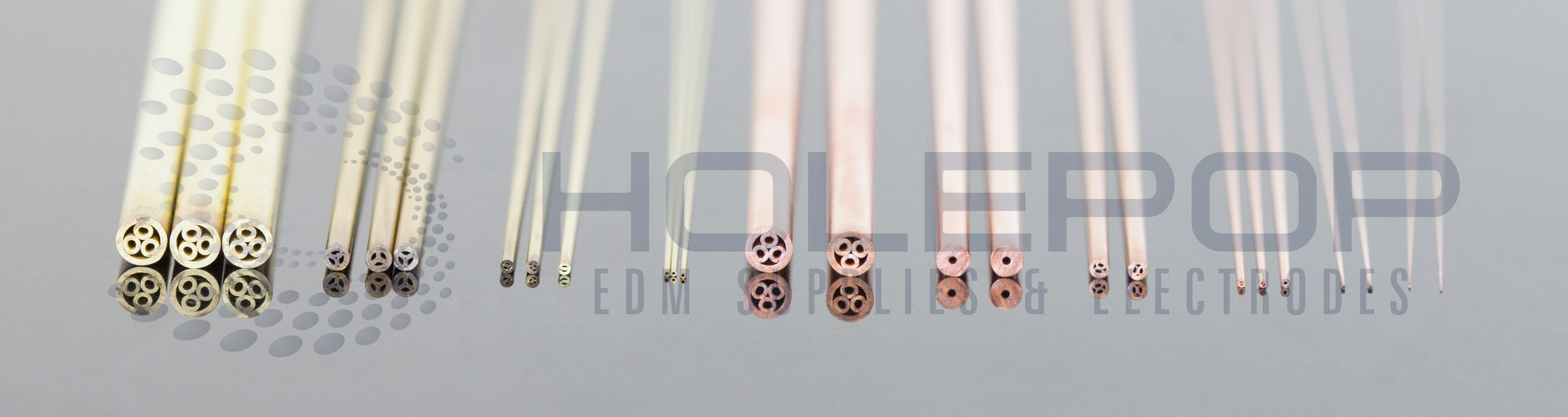
The following electrode types are available. Click on each to learn more about its applications and specifications:
Brass EDM Electrodes
– Key Features: Fast drilling speeds, low cost, and versatility.
– Best For: General-purpose applications where extremely hard materials are not involved.
– Limitations: Higher wear rate, less suited for machining tough materials.
Copper EDM Electrodes
– Key Features: High drilling power and better durability compared to brass.
– Best For: Applications requiring greater strength, such as machining tungsten carbide.
– Advantages: Cost-effective with enhanced performance for hard materials.
Tungsten Carbide EDM Electrodes
– Key Features: Exceptional hardness and durability.
– Best For: Machining exotic materials like Hastelloy, niobium, and other superalloys.
– Limitations: Higher cost but unmatched performance in demanding applications.
Copper Tungsten EDM Electrodes
– Key Features: Combines copper’s conductivity with tungsten’s hardness.
– Best For: Stress-testing applications and machining delicate parts.
– Advantages: High precision and available in sheet or foil form.
Pure Tungsten-Wolfram EDM Electrodes
– Key Features: Exceptional resistance to wear and high temperatures.
– Best For: High-stress applications requiring superior durability.
Other EDM Components
In addition to electrodes, EDM small hole drilling requires other critical components to ensure precision, efficiency, and optimal performance.
Here are some of the most commonly used EDM supplies:
EDM Electrode Guides
These guides ensure accuracy and stability during the drilling process, preventing deviations and enhancing precision.
Dielectric Fluid
Dielectric fluids are essential for flushing debris and maintaining proper electrical conductivity during EDM processes.
EDM Chucks
Chucks securely hold workpieces in place during machining, enabling precise and stable drilling operations.
Why Choose Holepop for EDM Solutions?
At Holepop, we specialize in providing high-quality EDM supplies and custom machining solutions designed to meet the unique demands of your business.
With years of experience and a commitment to innovation, Holepop is your trusted partner for all things EDM.
- Extensive Product Range: From tungsten carbide electrodes to dielectric fluids, we offer a comprehensive selection of EDM supplies to meet diverse industry needs.
- Customization Options: Our team works closely with you to provide custom solutions tailored to your specific machining requirements.
- Commitment to Quality: We source and manufacture only the highest quality components to ensure reliable performance and precision in your operations.
- Expert Support: Our knowledgeable team is here to assist with product selection, troubleshooting, and technical advice.
- Quick Turnaround Times: We understand the importance of timely delivery, ensuring you have what you need when you need it.
Ready to elevate your machining processes?
Contact Us today to discuss your needs, or explore our range of EDM products to see how Holepop can support your business.
Explore Our Products