High-Precision EDM Electrode Guides
Ceramic, Sapphire, and Silicon Nitride EDM Guide Characteristics
The importance of precise tolerances in a guide’s measurements cannot be overstated. Any slight deviation in a guide can amplify the imperfections in the electrode it holds, making the internal diameter of the guide critical—it must slightly exceed the diameter of its corresponding electrode. A fit that is too snug can hinder insertion, while one that is too loose can lead to inaccuracies in the drilled material. At Holepop, we customize guides to your exact requirements, ensuring the internal diameters of our electrode guides find the perfect balance between being too tight and too loose, guaranteeing that your electrodes hit their mark every time. However, achieving precision in perpendicular drilling is one thing; angling introduces its own set of challenges.
This is where guide geometry becomes crucial. Accuracy can falter when an electrode extends significantly from its guide, particularly at steep angles. This issue can be mitigated with a guide featuring a long, tapered tip. Our EDM guides are designed with versatility in mind, offering adjustable geometries to meet the needs of any task at hand. Yet, even the most meticulously crafted custom guides are subject to wear and tear. The resilience of a guide, therefore, is vital. This brings us to the materials at the heart of guide construction: traditional ceramic, sapphire, and silicon nitride. Each offers unique benefits in terms of durability, ensuring that our guides not only meet but exceed performance expectations in even the most demanding applications.
Ceramic Vs. Sapphire Vs. Silicon Nitride
Conventional Ceramic Guides
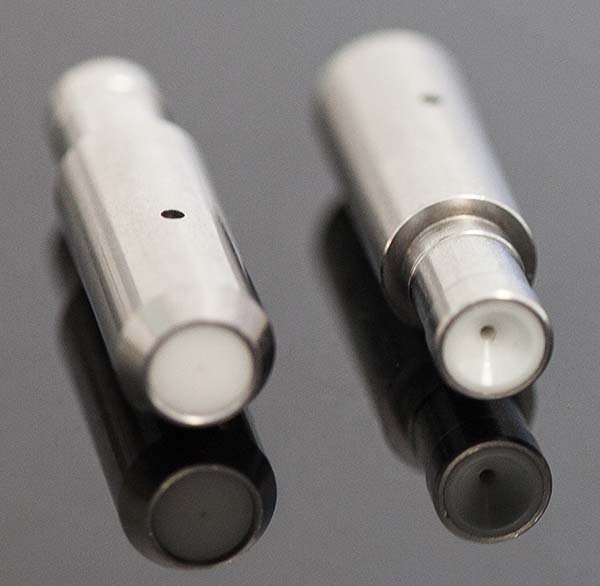
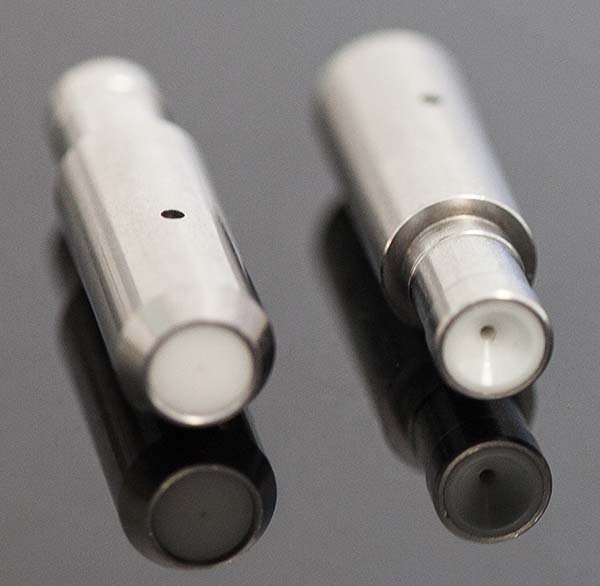


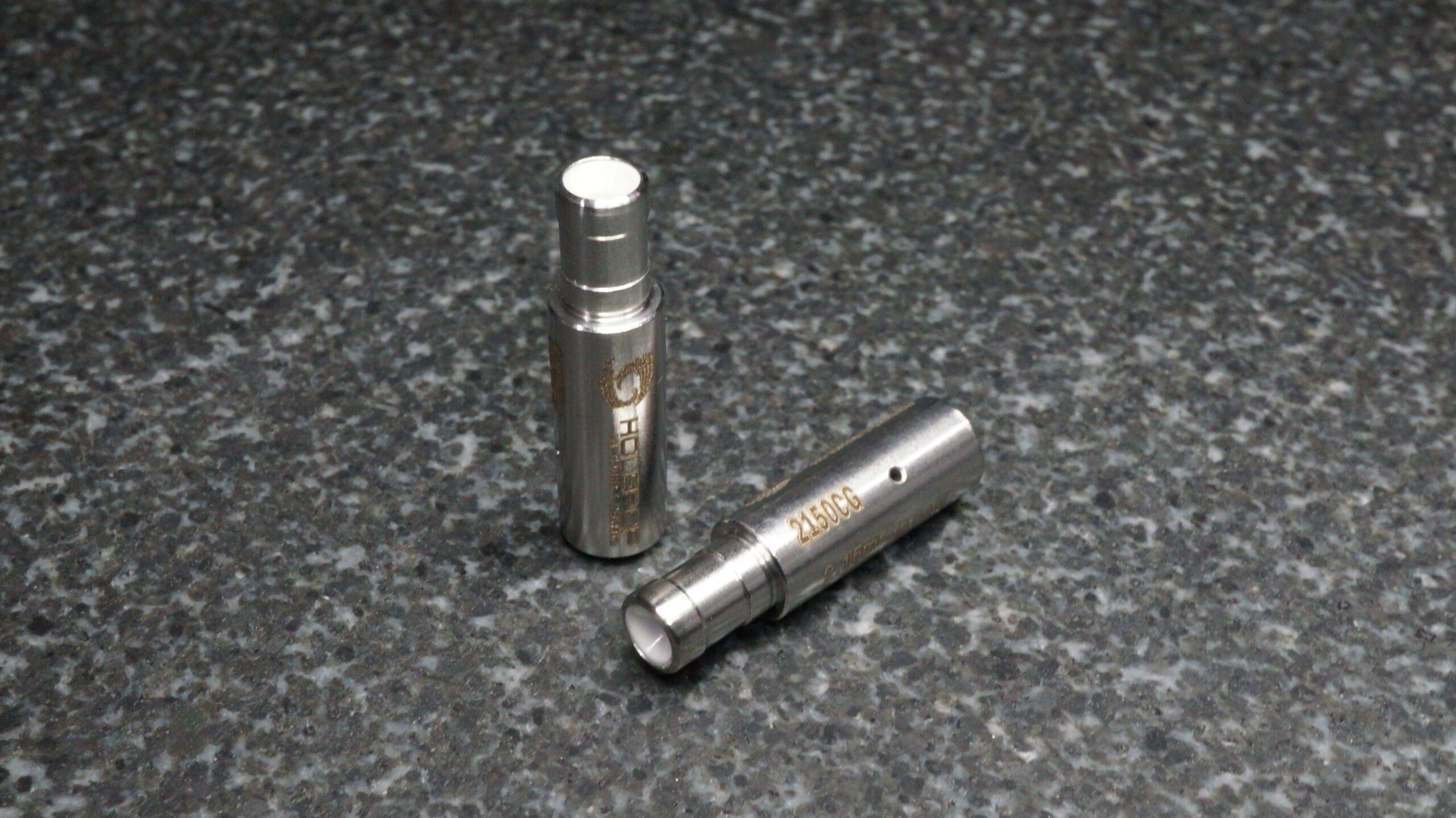
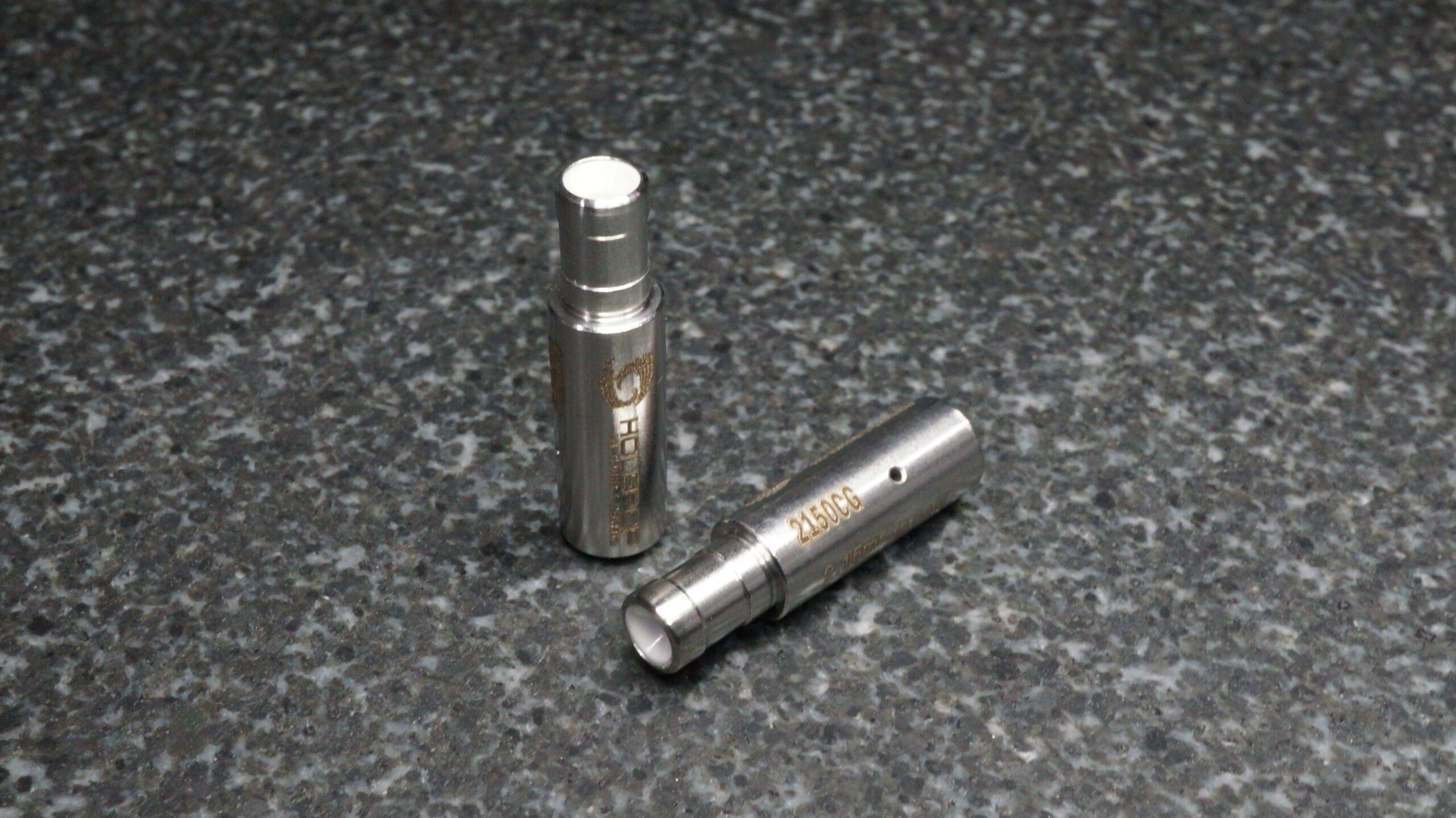
Ceramic guides are known for their robustness, maintaining tight tolerances and withstanding high temperatures.
These guides offer a balance between performance and affordability, making them suitable for various applications.
Ideal for short production runs, ceramic guides are often available in standard sizes and configurations.
Sapphire Guides
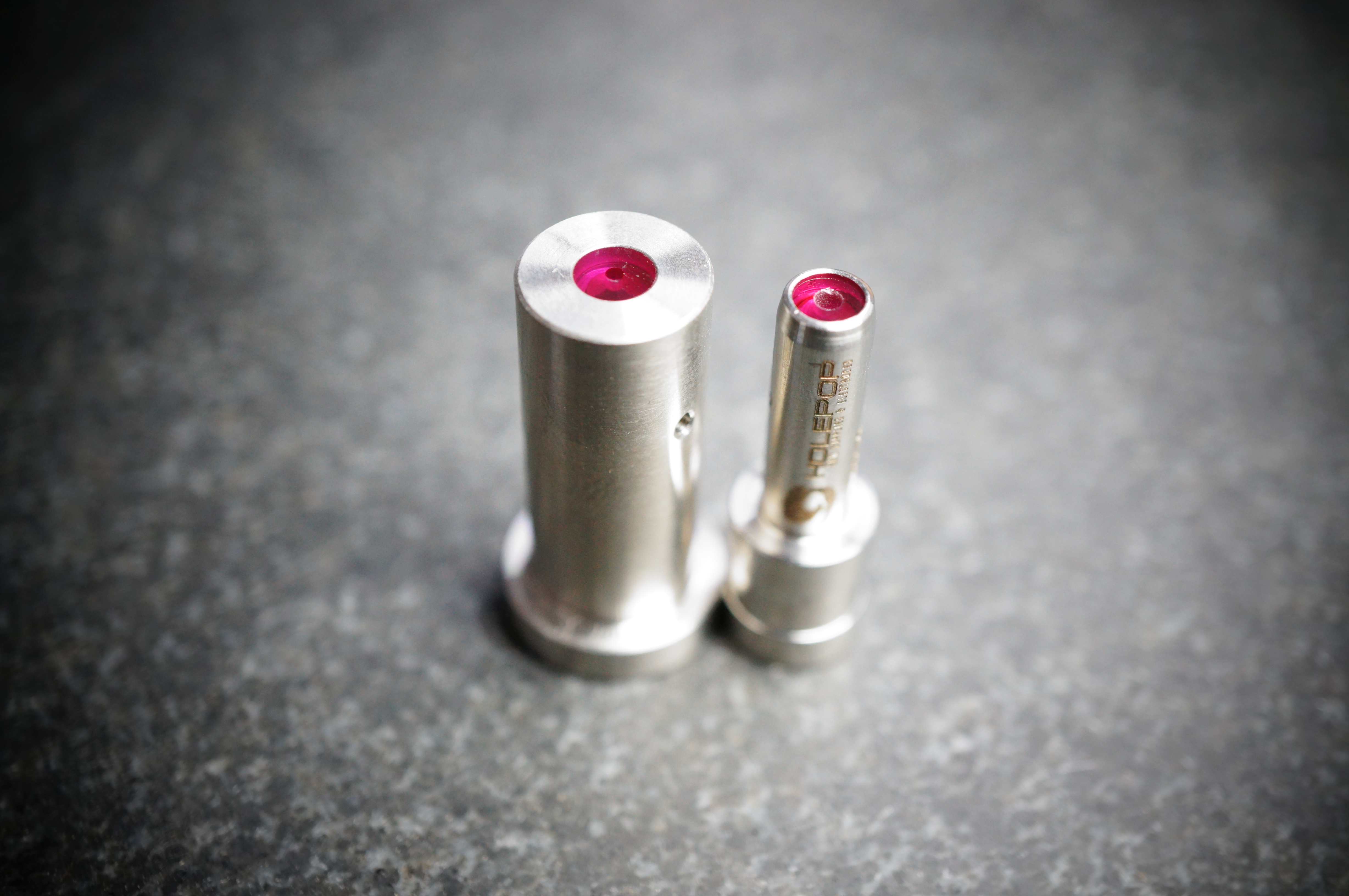
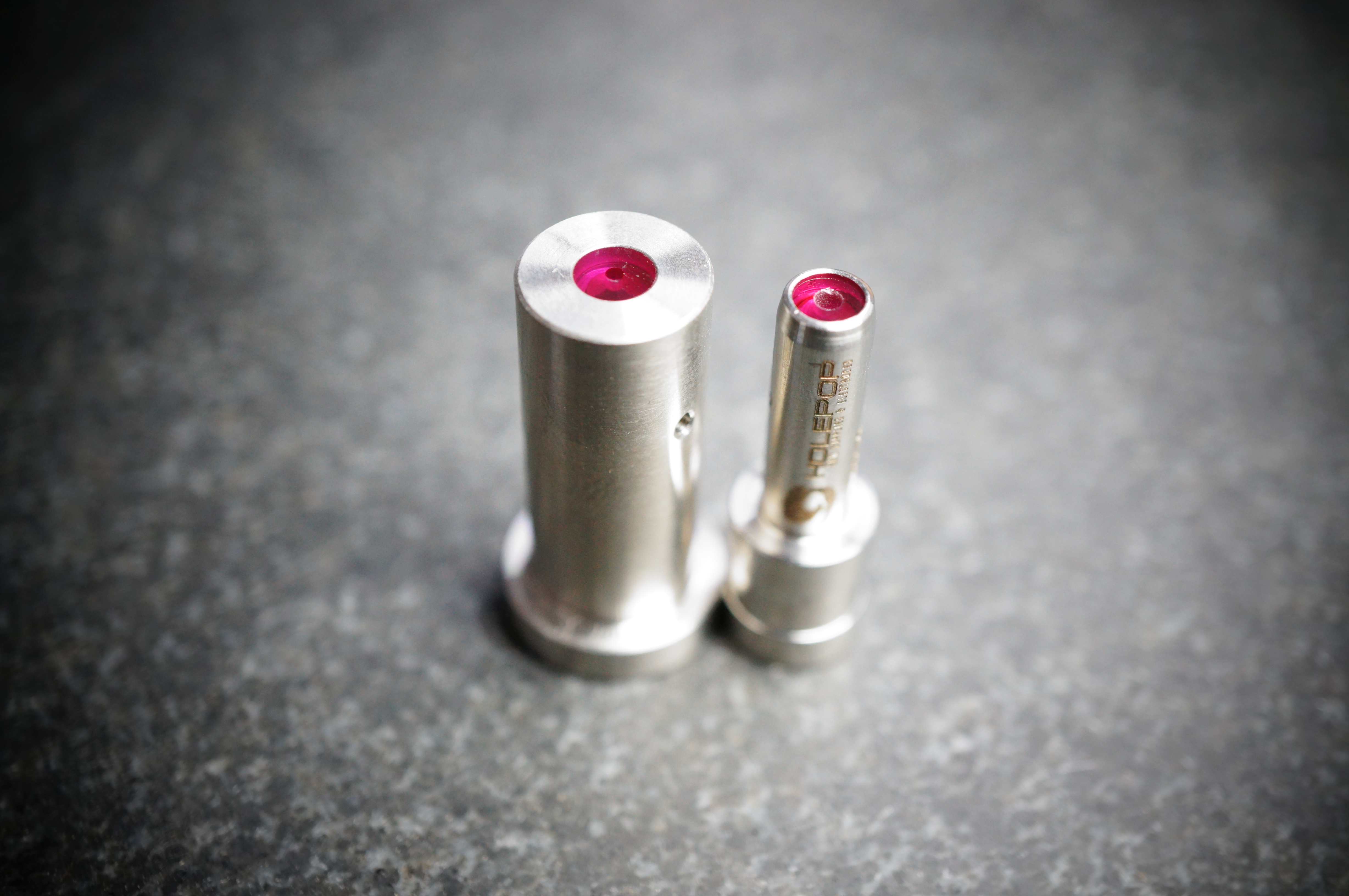
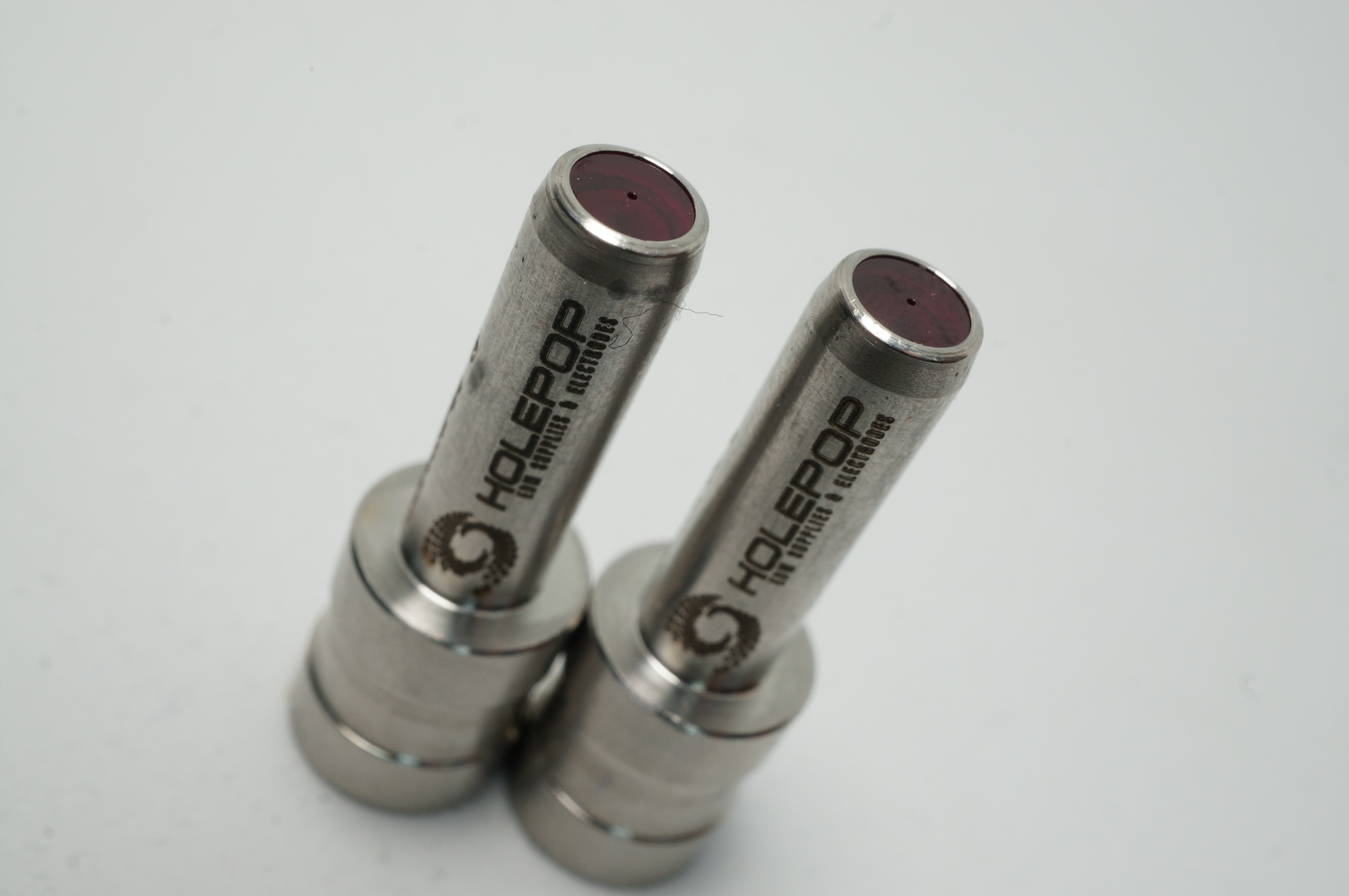
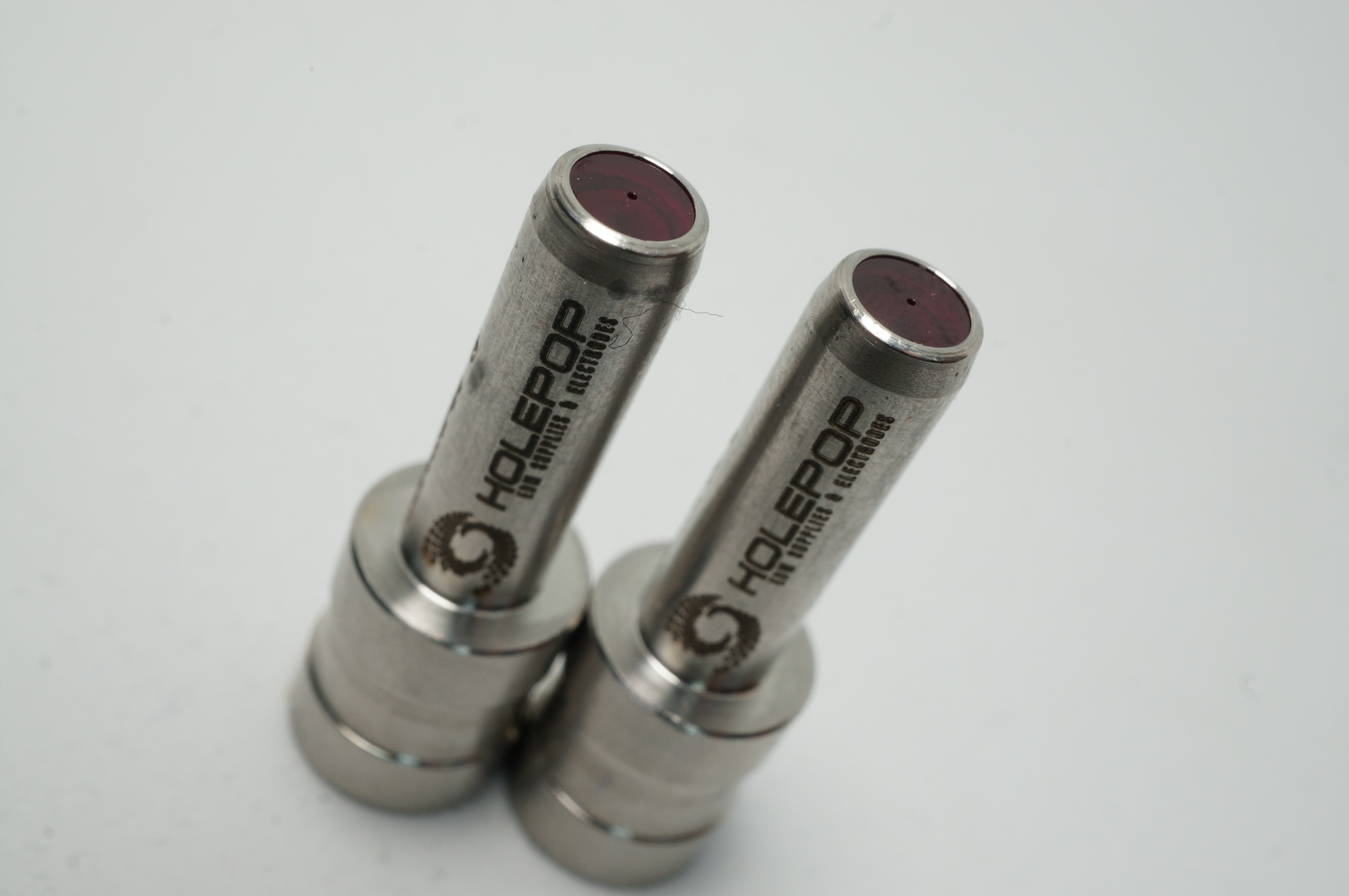
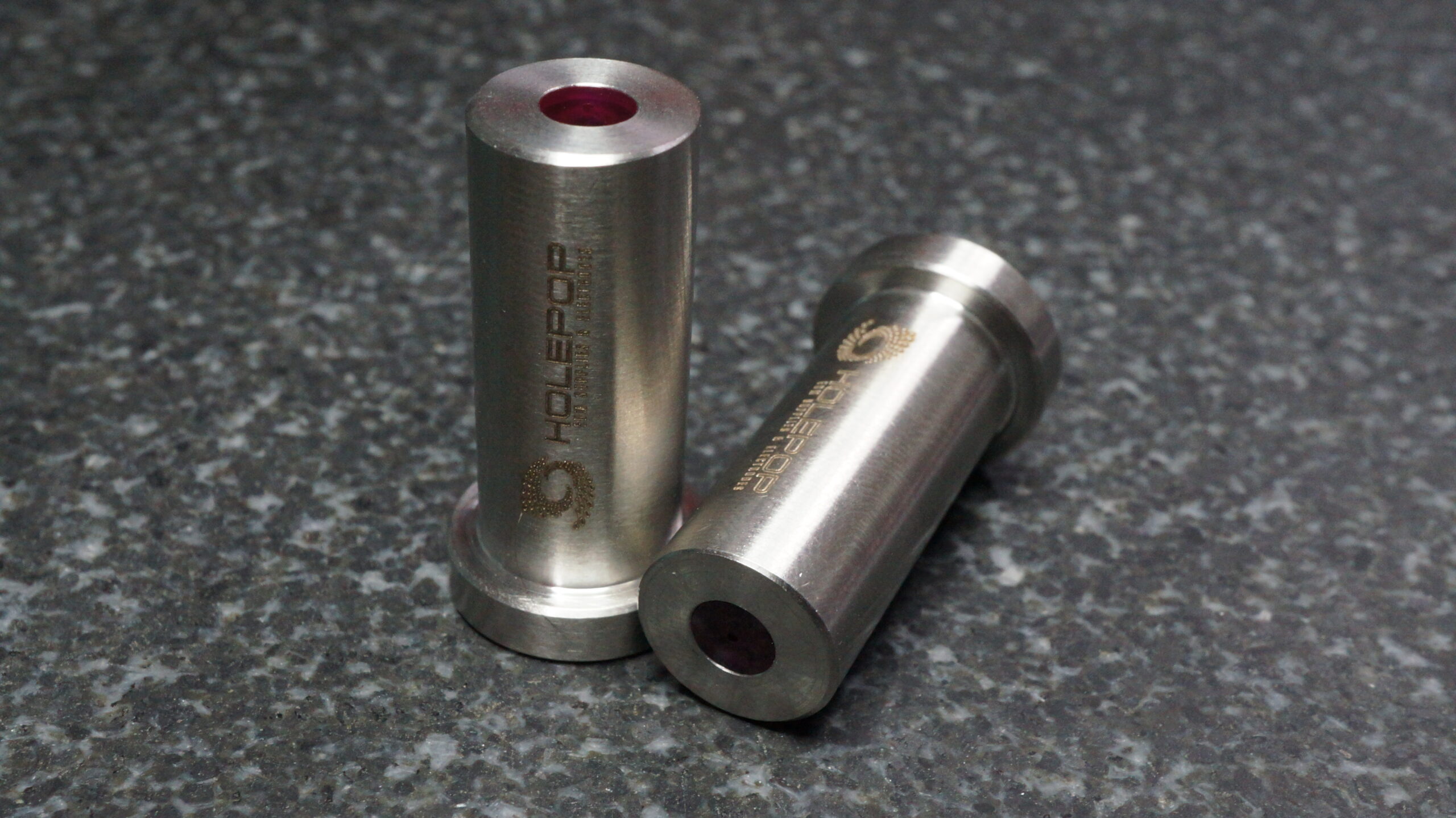
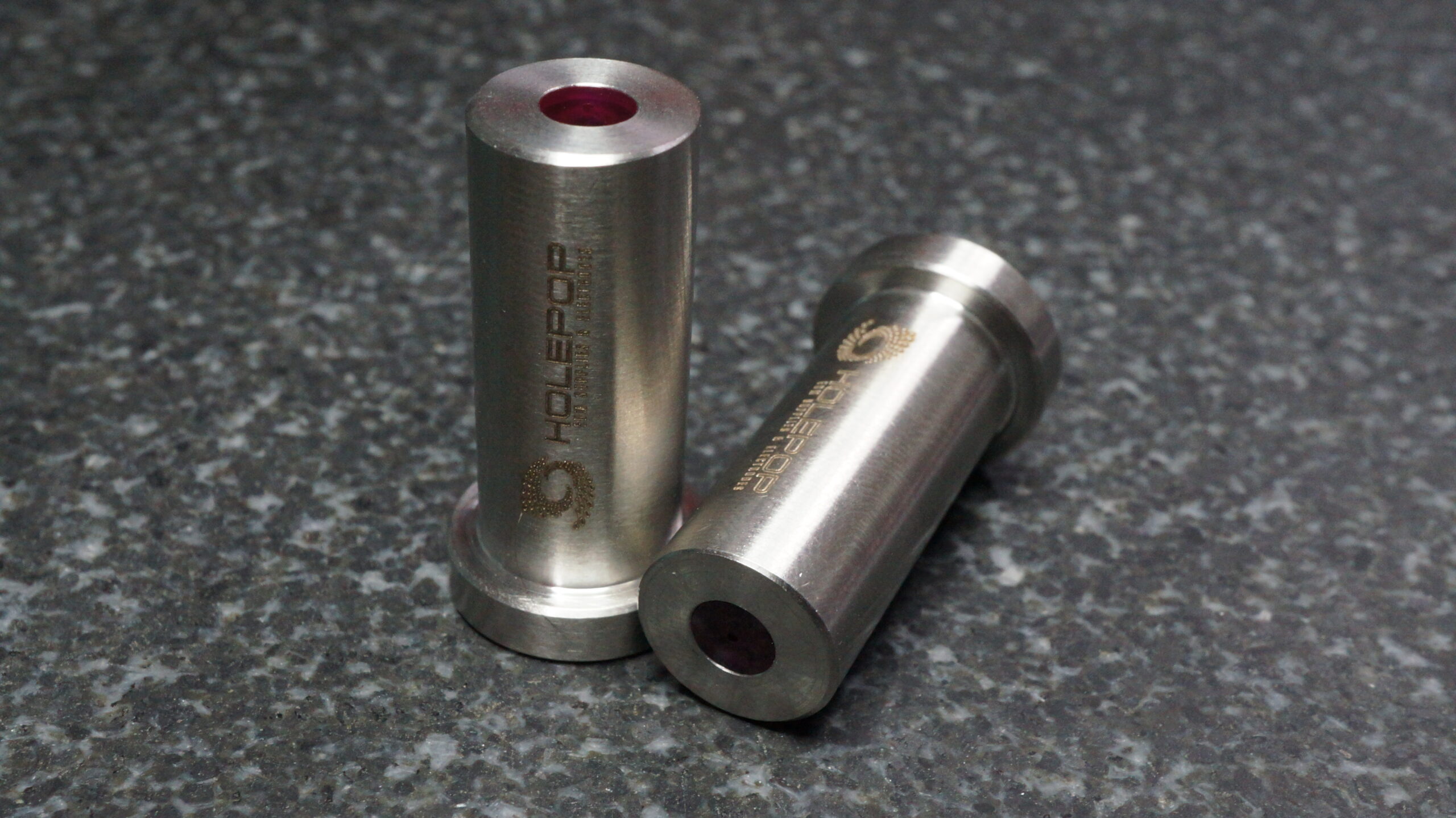
Sapphire guides provide exceptional hardness and wear resistance, ensuring long-lasting precision.
With low friction and excellent thermal stability, they are ideal for high-accuracy EDM processes.
Commonly used in industries requiring detailed machining, sapphire guides reduce operational costs over time.
Silicon Nitride Guides
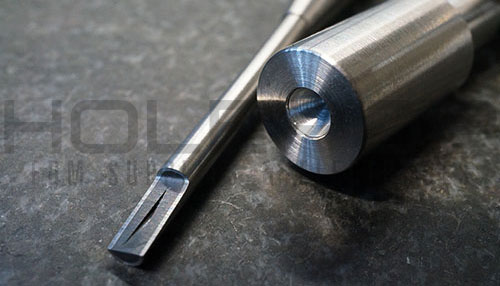
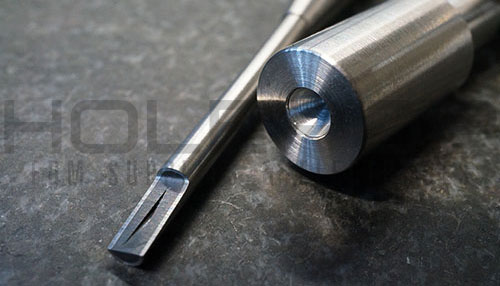
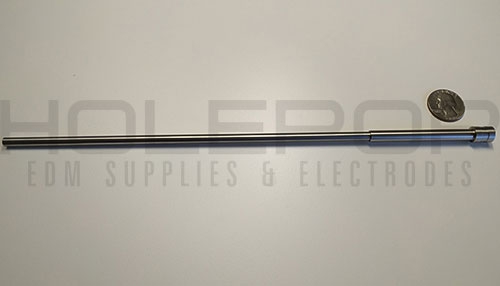
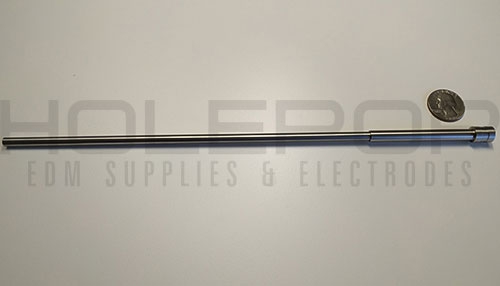
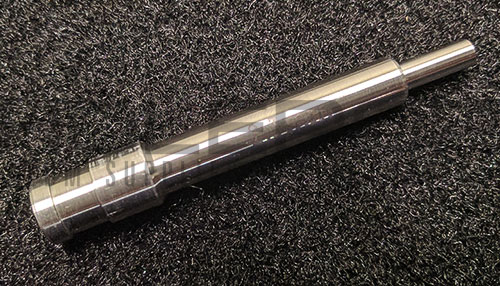
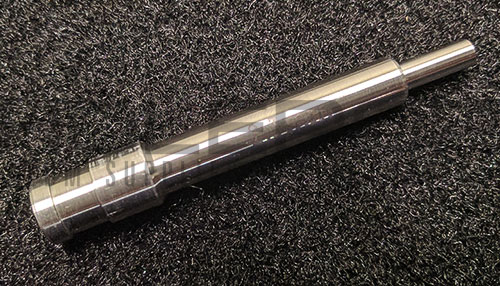
Silicon nitride guides offer superior durability with minimal thermal expansion and exceptional resistance to wear.
The low porosity and smooth surfaces reduce friction and improve the lifespan of both guide and electrode.
Designed for high-demand applications, silicon nitride guides enhance precision and efficiency in EDM tasks.
GF / Agie-Charmilles Guides and Guide Sets
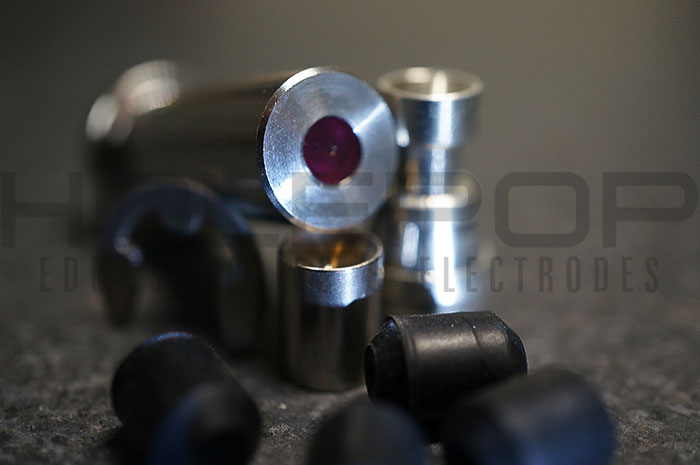
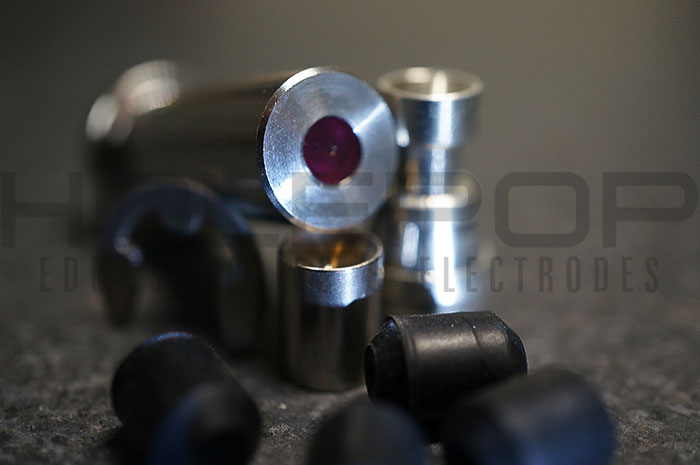
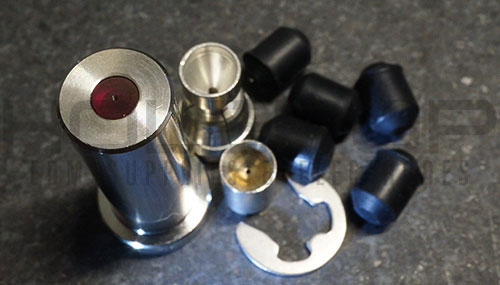
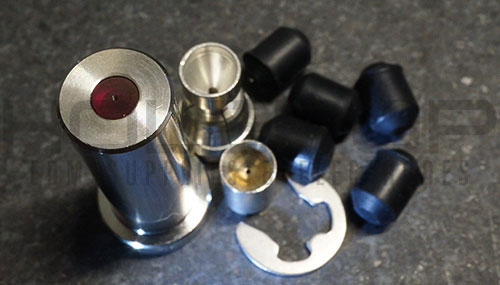
The Agie-Charmilles series is renowned for incorporating sapphire in EDM guide construction, celebrated for exceptional hardness and resistance to wear.
These guides ensure low friction, superior surface finishes, and precise wire positioning over extended machining periods.
Our guide sets, designed for Agie-Charmilles 054-0014 series machines, include collets, compression sleeves, and customizable components to meet specific machining requirements.
By integrating these advanced guides, you enhance operational efficiency and quality, keeping your machining at the forefront of technological advancement.
SODICK EDM Guides






Sodick EDM guides enhance precision and stability in EDM systems, ensuring accurate wire positioning for superior machining results.
Crafted from materials like diamond and sapphire, they offer exceptional durability and reduce friction, improving wire longevity and performance.
Widely used in aerospace, automotive, and medical device manufacturing, these guides seamlessly integrate with Sodick EDM machines to enhance operational efficiency.
Visit Sodick’s Official Website for more details on these innovative EDM guides.
Current EDM RT/CT Series Guides
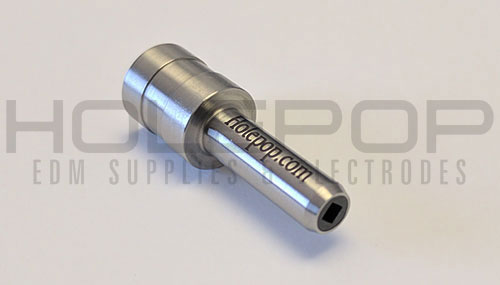
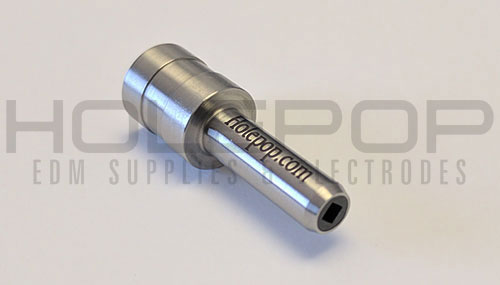
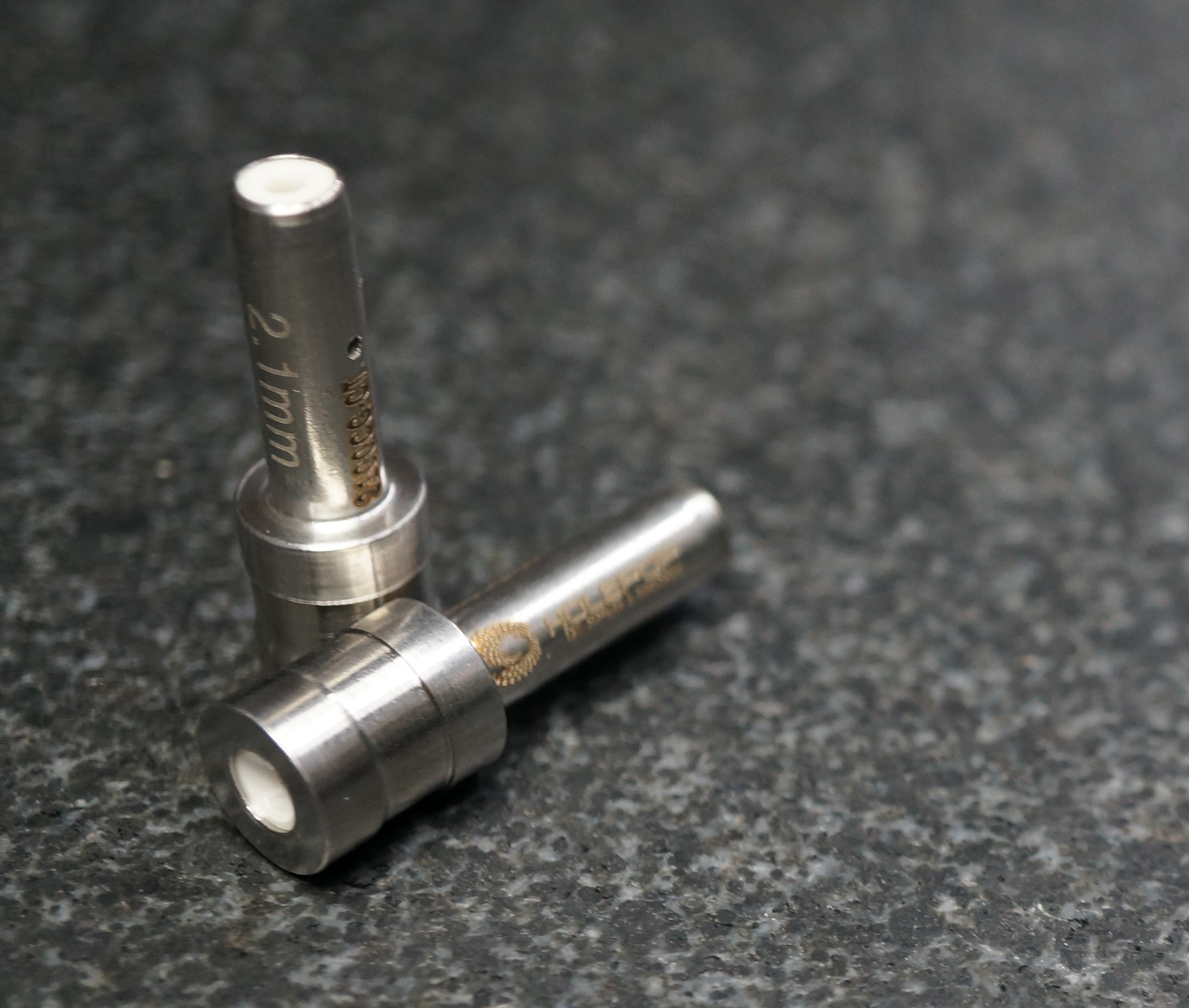
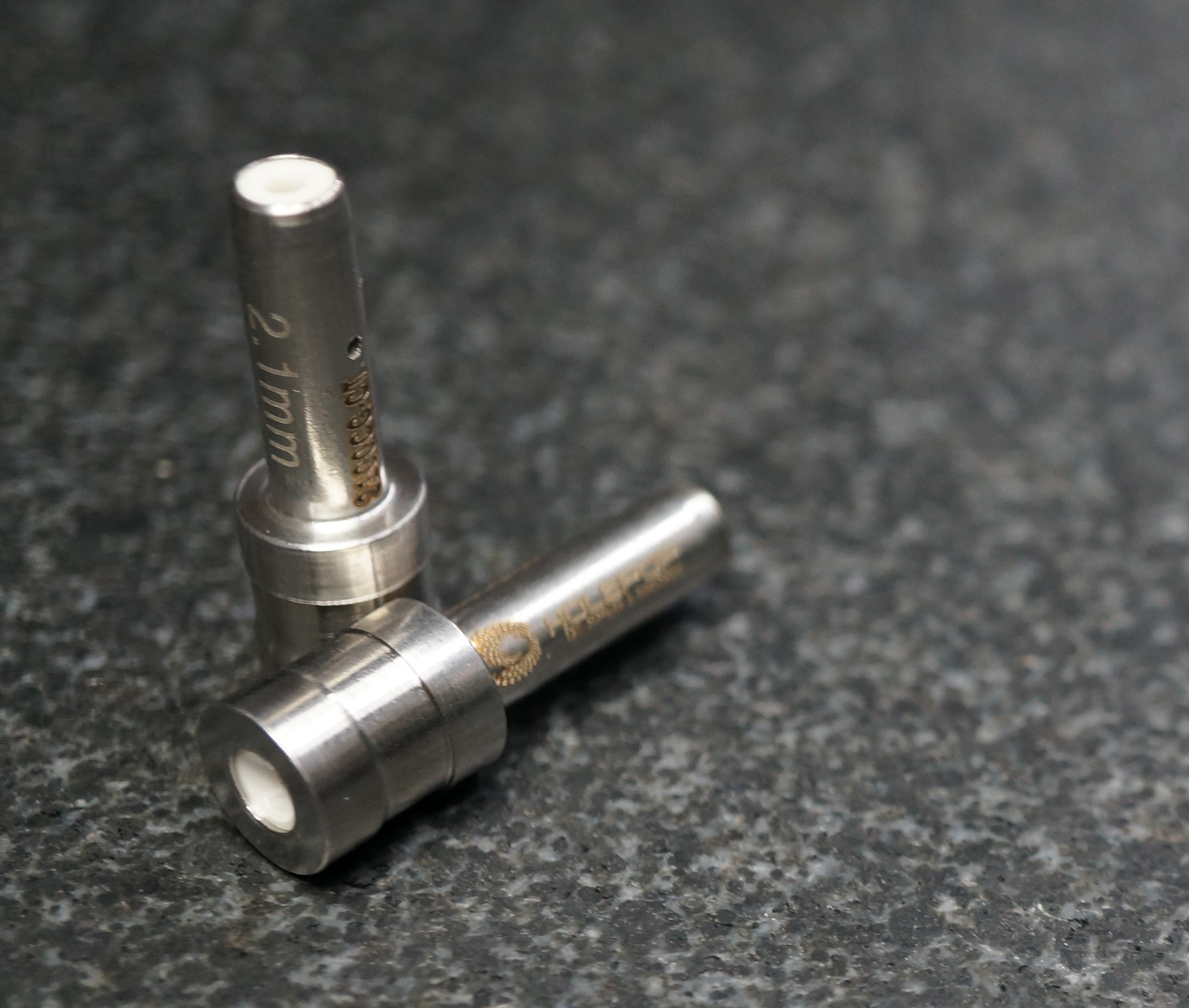
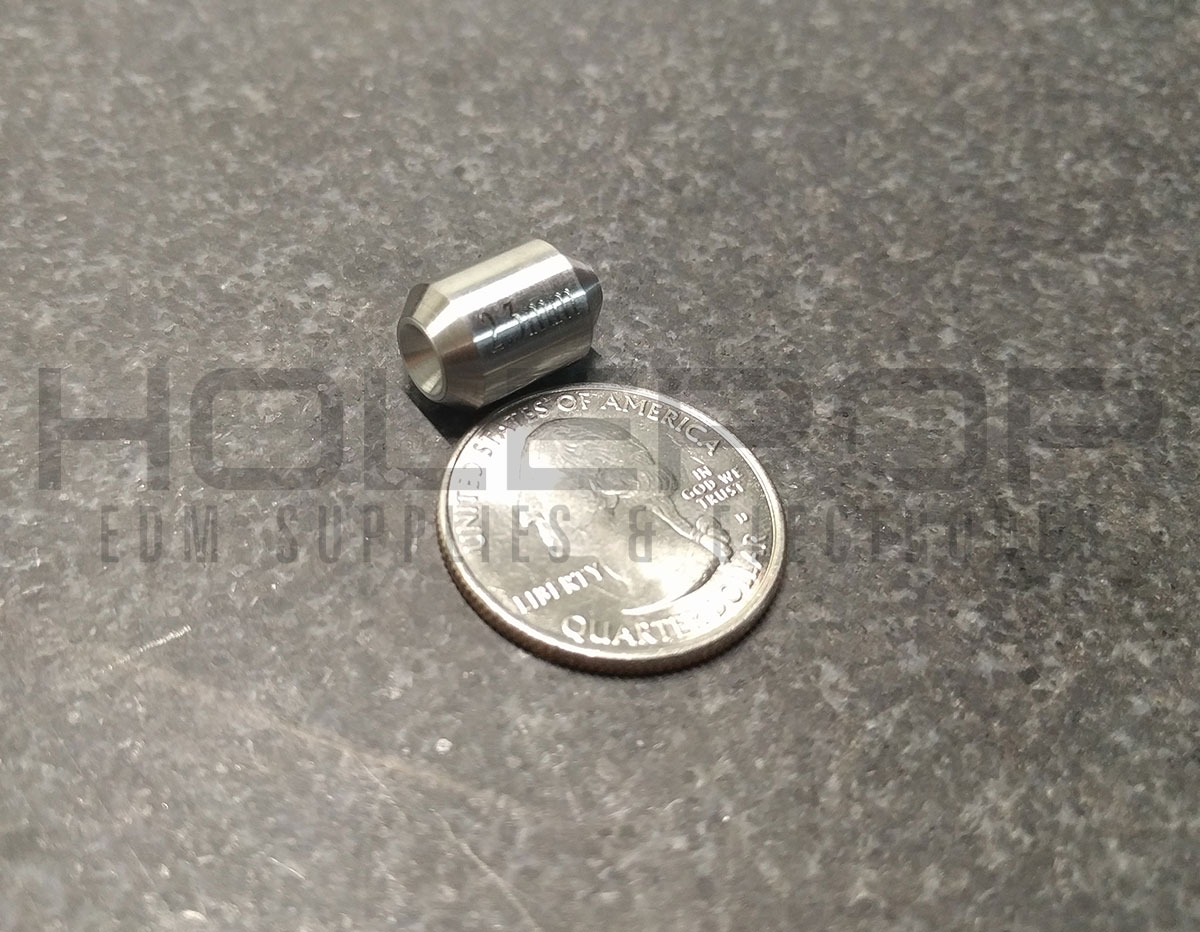
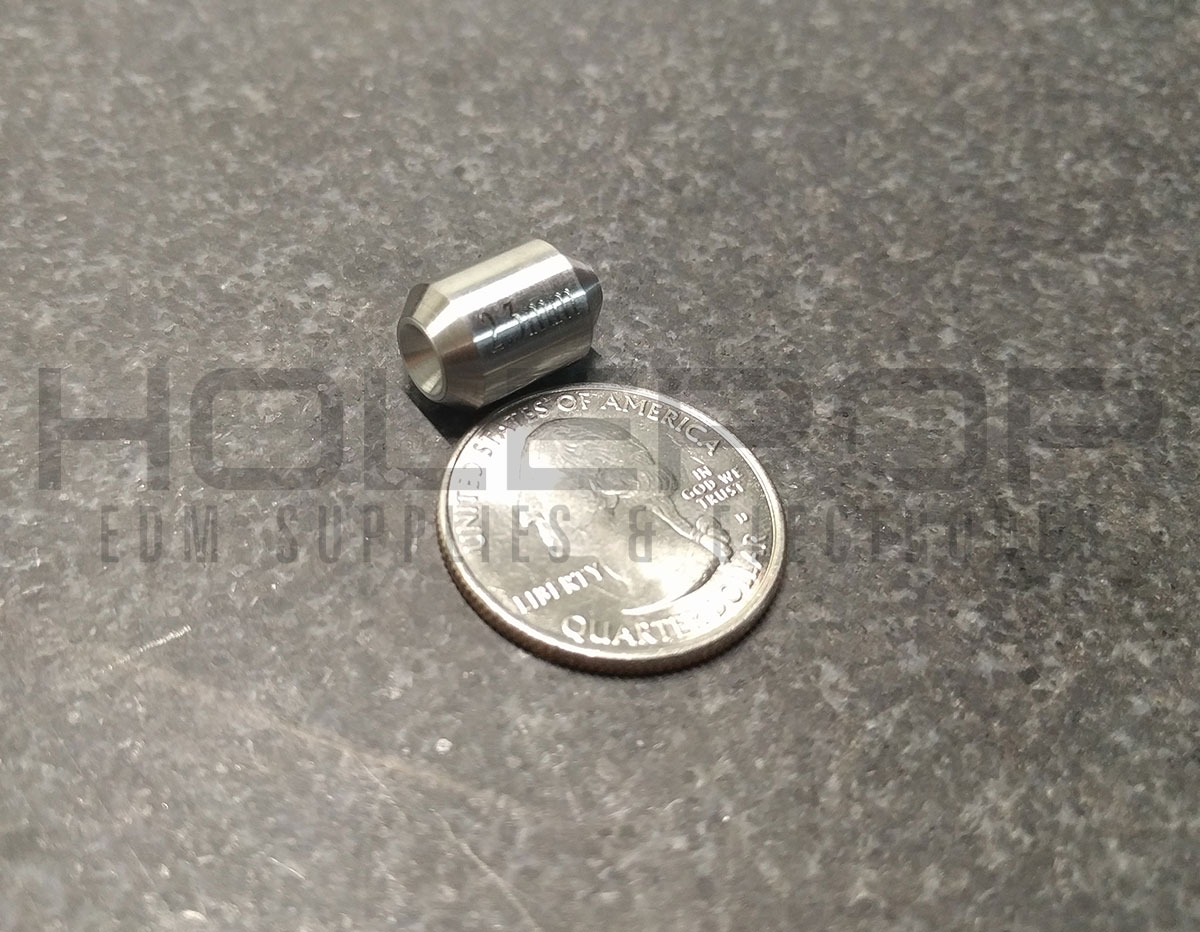
Our collection of Current EDM RT/CT Series guides is designed for precision and durability, catering to small hole drilling applications.
Available with ceramic or silicon nitride surfaces, these guides minimize wear and enhance efficiency in high-demand tasks.
The silicon nitride option provides superior thermal resistance and reduced friction, elevating your RT/CT Series machine’s performance.
Customizable dimensions ensure these guides meet your exacting machining standards for optimal performance.
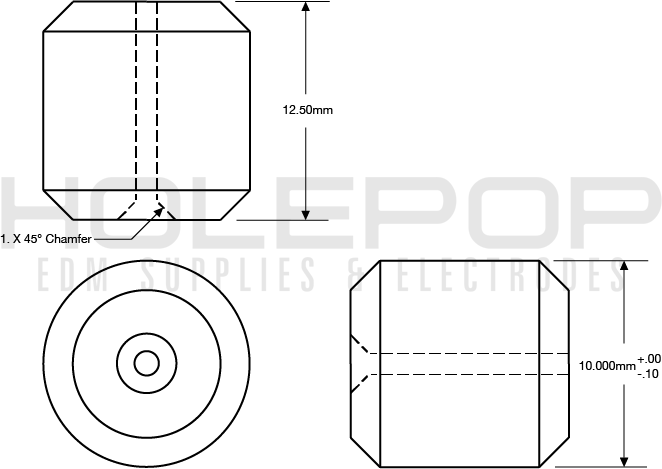
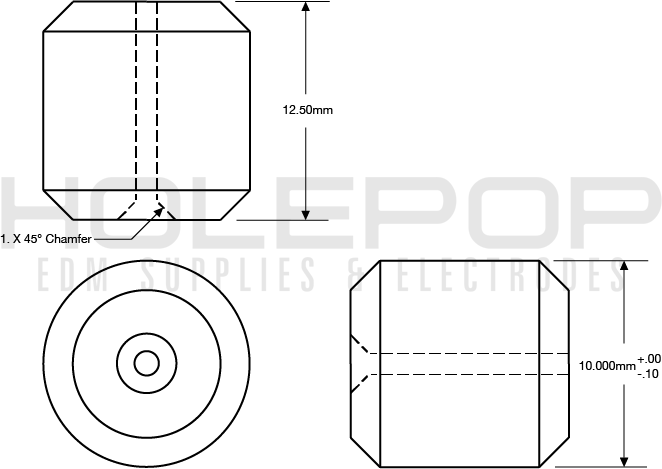