Versatile Applications of Copper Tungsten EDM
Overview
Copper tungsten, often referred to as tungsten copper, CuW, or WCu, is a pseudo-alloy combining copper and tungsten through a unique manufacturing process. This hybrid material integrates the distinct characteristics of both tungsten and copper, making it valuable in electrical discharge machining (EDM). With high strength, thermal conductivity, and precision, copper tungsten is ideal for applications across aerospace, defense, automotive, and semiconductor manufacturing.
Capabilities
High Precision Machining
Copper tungsten provides excellent stability and precision, minimizing tool walking and ensuring deep hole drilling in demanding applications.
Material Versatility
Its combination of copper’s conductivity and tungsten’s strength enables machining of materials impractical for brass or copper electrodes, making it suitable for various industries.
Customizability
Copper tungsten electrodes can be customized in size, length, and tungsten-to-copper ratio to meet specific machining requirements.
Applications
Aerospace Components
Precision machining of turbine blades and heat-resistant components for the aerospace industry.
Automotive Parts
Manufacturing durable and efficient parts for high-performance vehicles.
Defense Systems
Critical components for military-grade equipment, offering unmatched reliability and precision.
Semiconductor Manufacturing
Precision tools for producing micro-components in semiconductor and electronics industries.
Silicon Wafer Production with Copper Tungsten
Copper tungsten plays a vital role in silicon wafer production for semiconductor manufacturing. Leveraging EDM technology, it facilitates:
- Micro-drilling and etching for intricate wafer designs
- Precision slicing for consistent wafer thickness
- Thermal and electrical stability for machining advanced materials
Learn more about our Silicon Wafer Production capabilities.
Copper Tungsten Foil


Copper tungsten foil is an exceptional material known for its unique combination of tungsten’s strength and high melting point with copper’s excellent thermal and electrical conductivity. This makes it extremely effective in environments that demand resistance to high temperatures and corrosion while requiring superior electrical and thermal performance.
Copper Tungsten Single Hole EDM Tubes


Copper Tungsten Single Hole EDM Tubes are precision-engineered tools designed for optimal performance in EDM drilling applications. Combining copper’s excellent electrical conductivity with tungsten’s high melting point and mechanical strength, these tubes provide superior heat resistance and stability.
Copper Tungsten EDM Rods
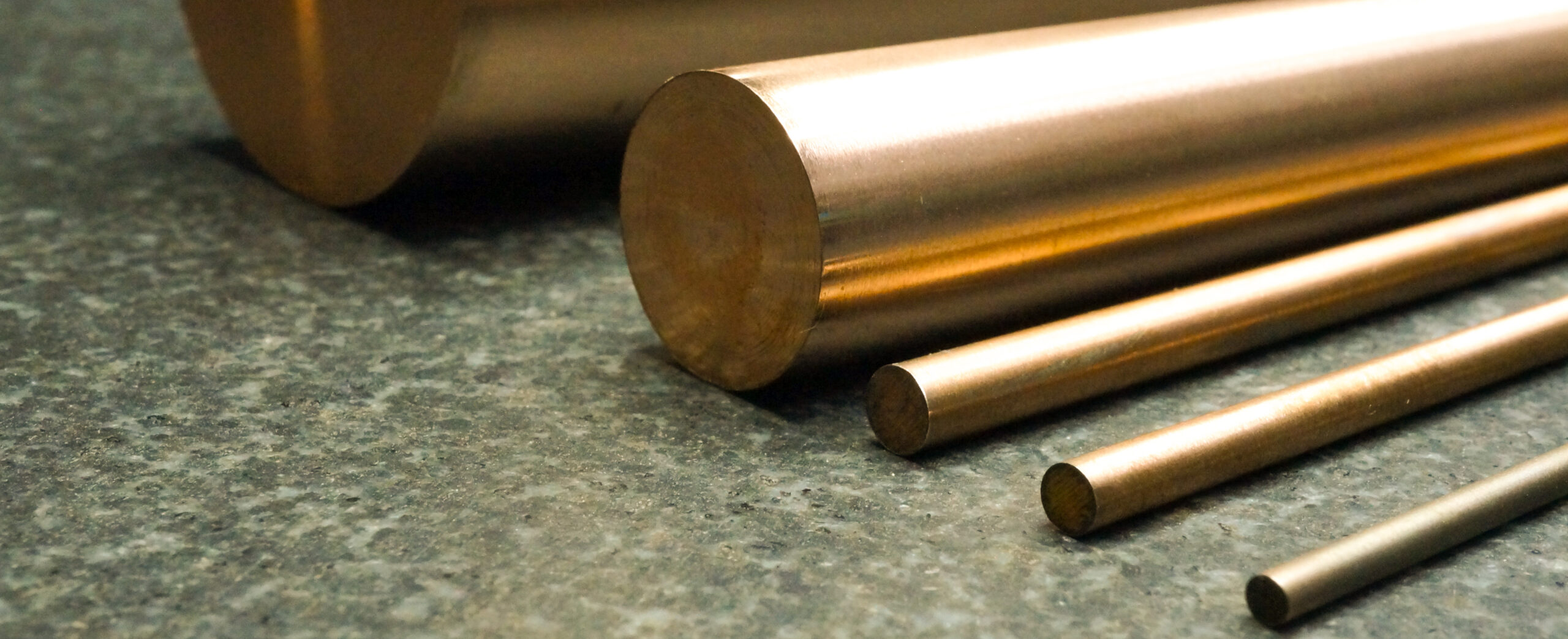
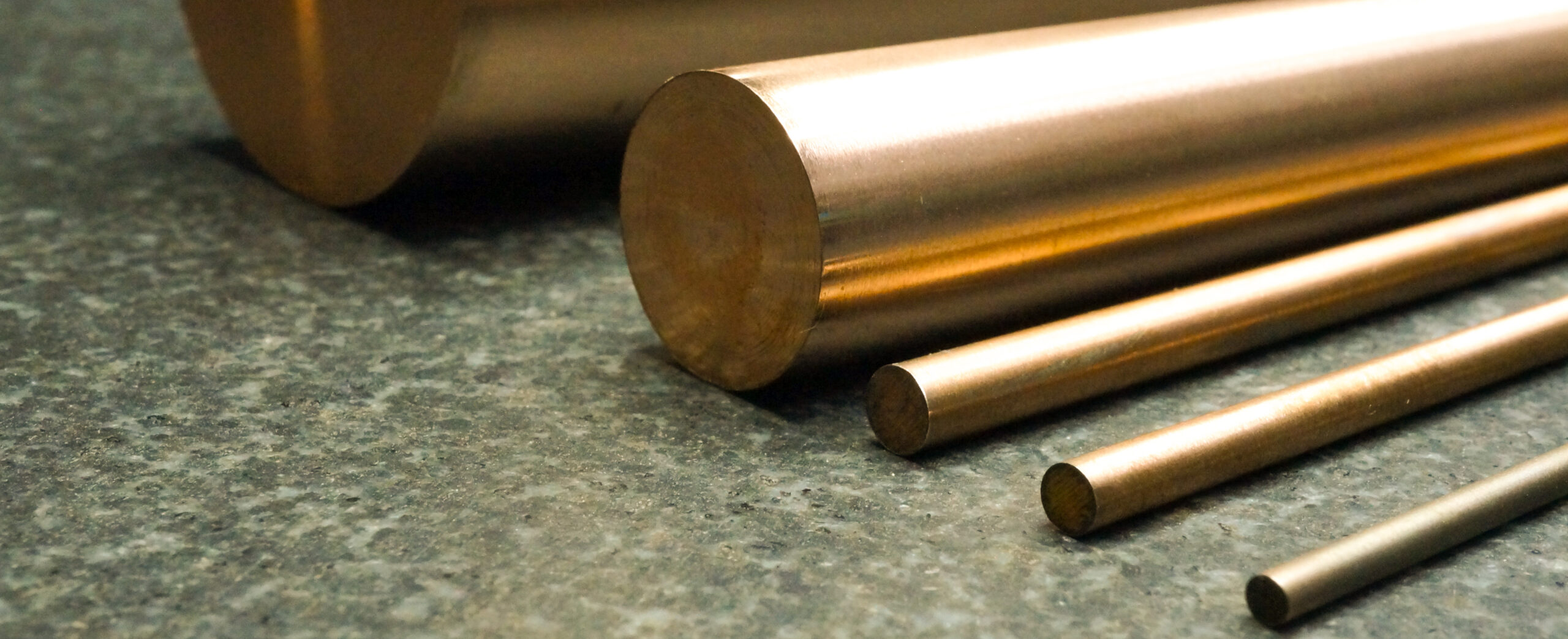
Copper Tungsten EDM Rods are essential for high-precision electrical discharge machining, offering a unique combination of tungsten’s hardness and high temperature resistance with copper’s superior electrical and thermal conductivity.
Copper Tungsten Blocks
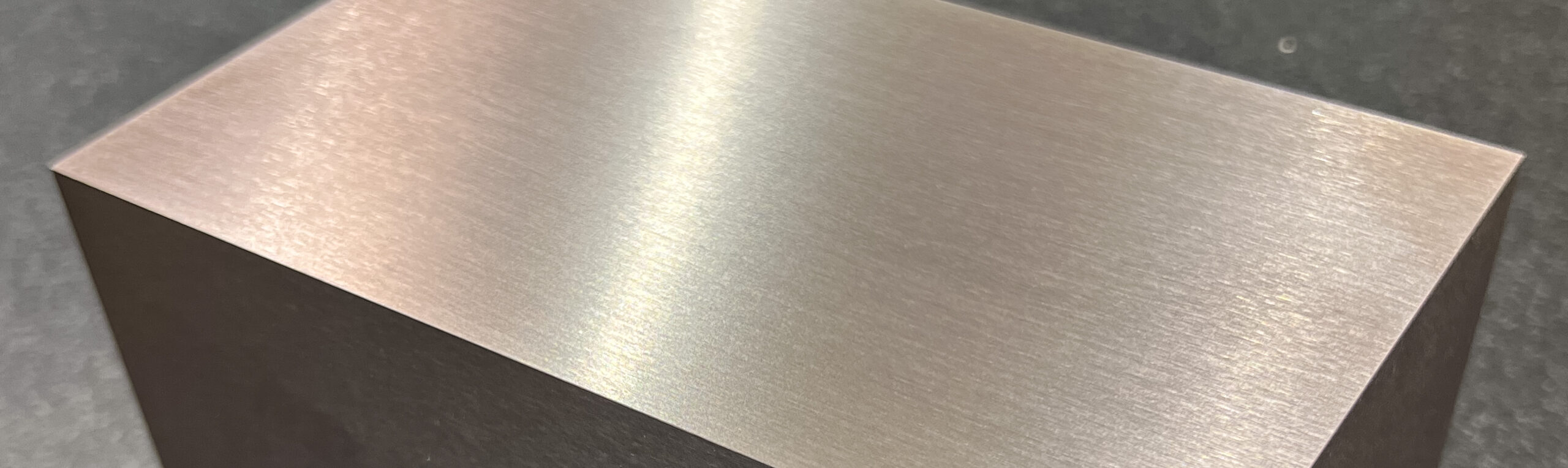
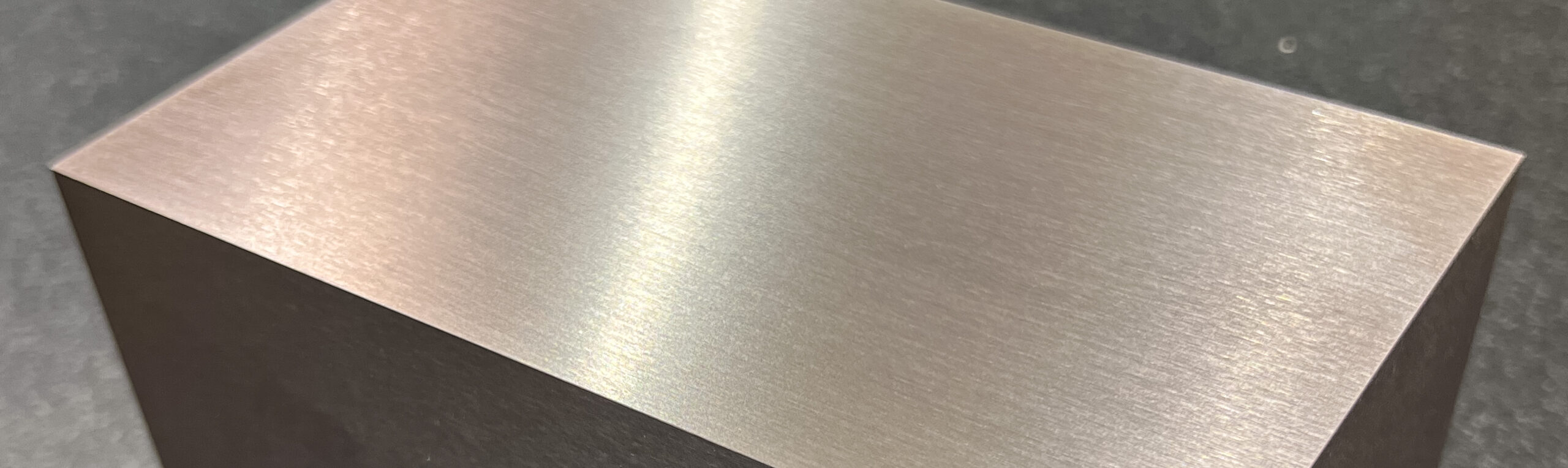
Copper Tungsten Blocks combine copper’s excellent thermal and electrical conductivities with tungsten’s exceptional strength and heat resistance, making them ideal for uses in electrical contacts, heat sinks, and heavy-duty machining components.
Copper Tungsten Plates
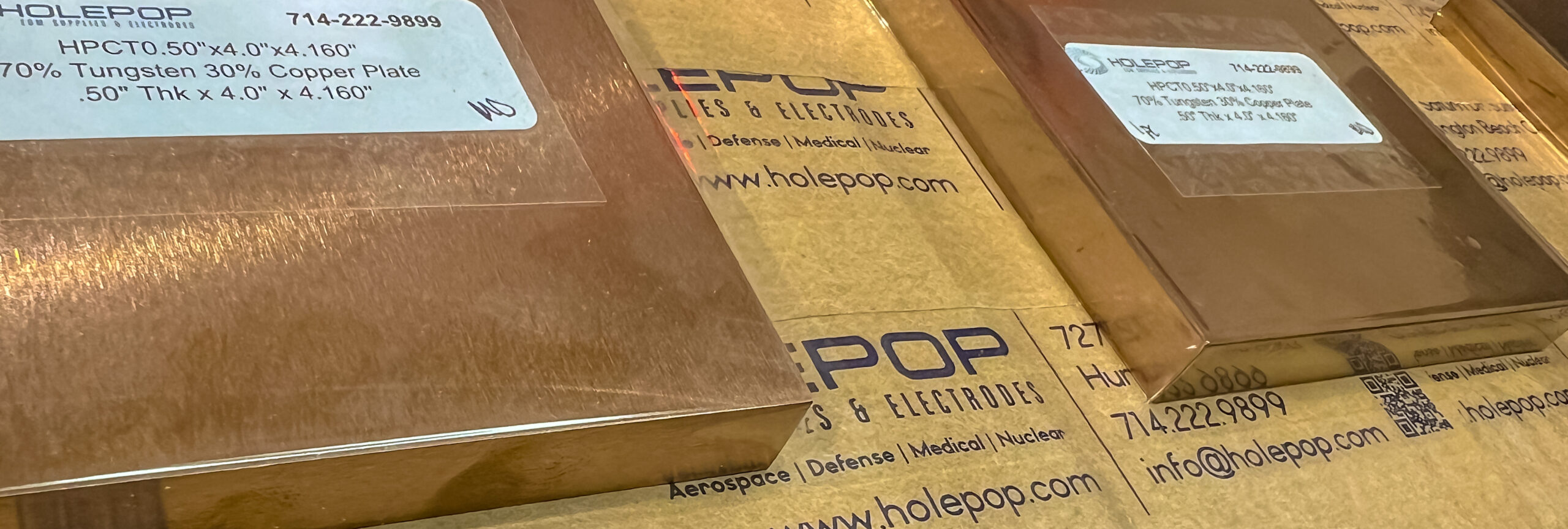
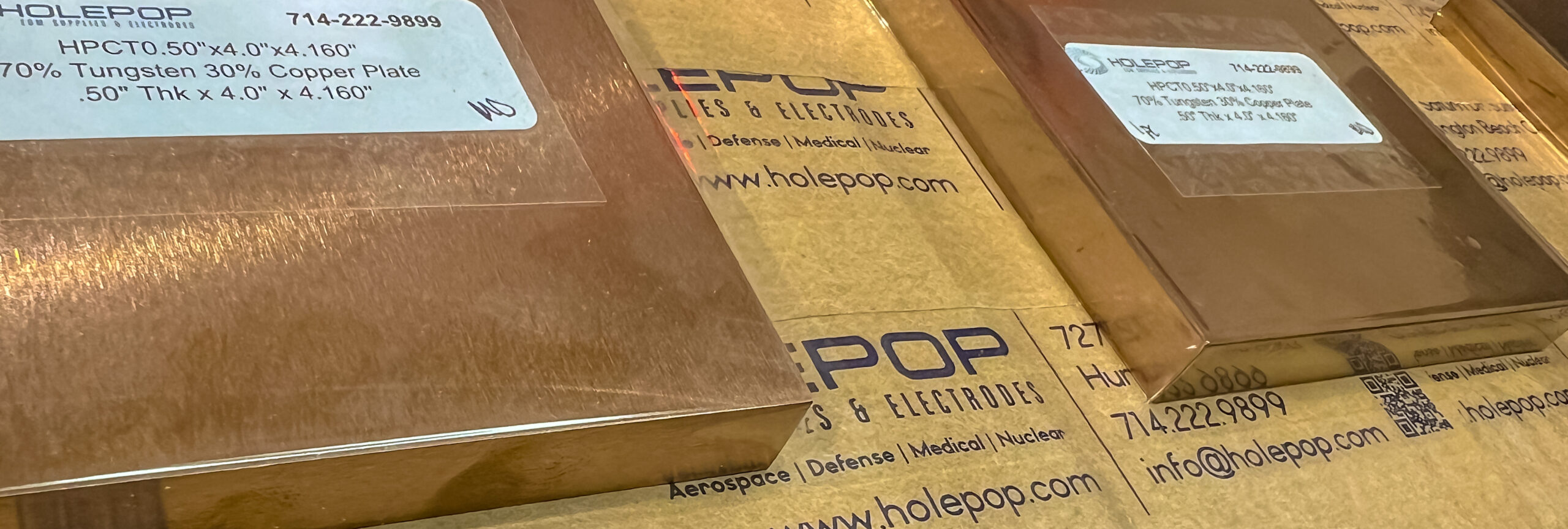
Copper Tungsten Plates are engineered to offer outstanding performance in applications that demand high thermal and electrical conductivity alongside excellent heat resistance.
Custom copper tungsten electrodes are available in sizes from .06mm (only rods are available from .06mm to .1mm) to
3.0mm in diameter, in lengths from 100mm to 700mm. Inner and outer diameters may be adjusted. The ratio of tungsten
to copper can be adjusted to optimize electrode characteristics. The percentage of tungsten is from 50% to 90%, with
10% gradations. Diameter gradations for copper tungsten are not as fine as those for brass or copper, due to
different manufacturing methods.
Contact Us
Leverage the capabilities of copper tungsten EDM electrodes for your next project. Contact Holepop today to learn how our expertise can optimize your manufacturing needs.